يعتمد مبدأ المطحنة الكروية على مجموعة من العوامل الميكانيكية والتشغيلية التي تعمل معًا لطحن المواد إلى جسيمات دقيقة.وتشمل المبادئ الرئيسية ما يلي التأثير و الاستنزاف حيث تصطدم الكرات الثقيلة داخل الطاحونة بالمادة لتفتيتها.وتتأثر كفاءة عملية الطحن بعوامل مثل أبعاد الأسطوانة، وسرعة الدوران، وحجم الكرة وكثافتها، وخصائص المادة، ونسبة ملء الطاحونة.ويضمن تحقيق السرعة الحرجة دوران الكرات على طول الجدران الداخلية، مما يؤدي إلى طحن المادة بفعالية.بالإضافة إلى ذلك، تلعب عوامل مثل وقت المكوث ومعدل التغذية وطبيعة مادة الطحن دورًا مهمًا في تحديد درجة الطحن.
شرح النقاط الرئيسية:
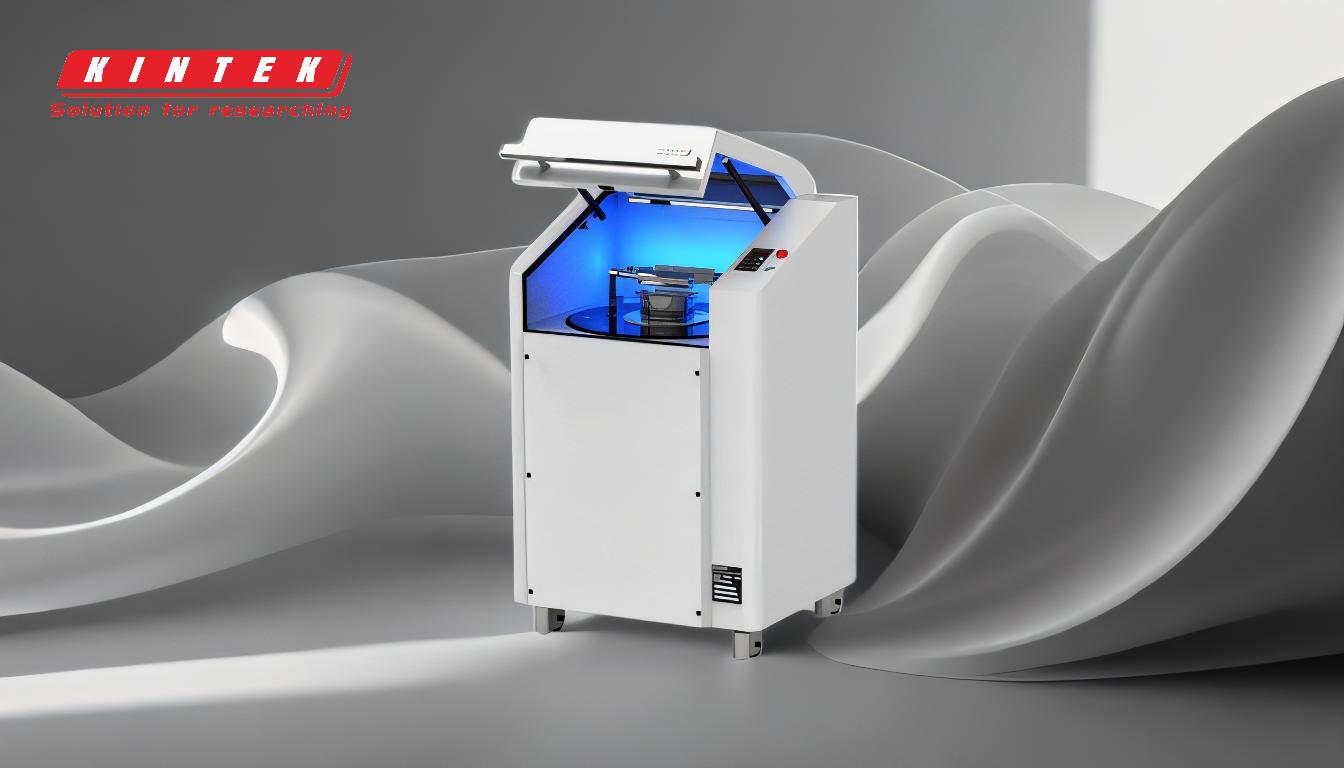
-
مبادئ التشغيل:التأثير والاستنزاف
- التأثير:ويحدث ذلك عندما تصطدم الكرات الثقيلة داخل المطحنة بالمادة، مما يؤدي إلى الضغط عليها وتكسيرها إلى جسيمات أصغر.
- الاستنزاف:يتضمن ذلك تقليل حجم المادة مع اصطدام الجسيمات بالكرات وبعضها البعض، مما يؤدي إلى جسيمات أدق بمرور الوقت.
- يعمل هذان المبدآن معًا لضمان الطحن الفعال، حيث يوفر الصدم التكسير الأولي والتآكل تنقية المادة بشكل أكبر.
-
السرعة الحرجة
- يجب أن تحقق الطاحونة الكروية سرعة دوران محددة، تعرف باسم السرعة الحرجة لضمان دوران الكرات على طول الجدران الداخلية للأسطوانة.
- تحت السرعة الحرجة، قد لا تولد الكرات قوة كافية لطحن المواد بفعالية.
- فوق السرعة الحرجة، قد تلتصق الكرات بالجدران بسبب قوة الطرد المركزي، مما يقلل من كفاءة الطحن.
-
أبعاد الأسطوانة وتصميمها
- قطر قطر الأسطوانة ونسبة نسبة قطر الأسطوانة إلى الطول (نسبة L:D) تؤثر بشكل كبير على الإنتاجية.
- نسبة L:D المثلى هي 1.56-1.64 يضمن كفاءة الطحن من خلال موازنة توزيع الكرات والمواد داخل المطحنة.
- يؤثر شكل سطح الدرع (البطانة الداخلية للأسطوانة) أيضًا على كفاءة الطحن من خلال التأثير على حركة الكرات.
-
وسائط الطحن:الكرات
- الكرات حجم وكثافة وعدد الكرات المستخدمة في المطحنة تلعب دورًا حاسمًا في تحديد كفاءة الطحن.
- فالكرات الأكبر حجمًا تكون فعالة في تكسير المواد الخشنة، بينما تقلل الكرات الأصغر حجمًا من المساحات الفارغة وتنتج جسيمات أدق.
- نسبة نسبة الملء (النسبة المئوية لحجم الطاحونة المملوءة بالكرات) يجب تحسينها لضمان الطحن الفعال دون تحميل الطاحونة أكثر من طاقتها.
-
خصائص المواد
- الخواص الخصائص الفيزيائية والكيميائية لمادة التغذية مثل الصلابة والكثافة ومحتوى الرطوبة، تؤثر على عملية الطحن.
- تتطلب المواد الأكثر صلابة مزيدًا من الطاقة والوقت للطحن، بينما قد يتم طحن المواد الأكثر ليونة بسرعة أكبر.
-
عوامل التشغيل
- سرعة الدوران:تؤثر السرعة التي تدور بها الأسطوانة على حركة الكرات وكفاءة الطحن.
- وقت الإقامة:يحدد مقدار الوقت الذي تقضيه المادة في حجرة الطحن درجة الطحن.
- معدل التغذية ومستواها:يجب التحكم في معدل تلقيم المواد في المطحنة ومستوى المواد في الوعاء للحفاظ على ظروف الطحن المثلى.
-
إزالة المنتج المطحون في الوقت المناسب
- تضمن الإزالة الفعالة للمواد المطحونة من المطحنة أن تظل عملية الطحن مستمرة وتمنع الإفراط في الطحن أو الانسداد.
- وهذا مهم بشكل خاص لتحقيق الدقة المطلوبة للمنتج النهائي.
-
العوامل التي تؤثر على أداء الطحن
- سرعة الدوران:يجب ضبطها لتحقيق السرعة الحرجة للطحن الأمثل.
- نوع وسيط الطحن:يتم استخدام الكرات أو القضبان الفولاذية بشكل شائع، مع تحديد حجمها وكثافتها بما يتناسب مع المادة التي يتم طحنها.
- طبيعة المادة:تحدد الصلابة والحجم والخصائص الأخرى للمادة الطاقة المطلوبة للطحن.
- نسبة الملء:يجب تحسين النسبة المئوية لحجم الطاحونة المملوءة بوسيط الطحن لتحقيق التوازن بين كفاءة الطحن واستهلاك الطاقة.
من خلال فهم هذه العوامل وتحسينها، يمكن زيادة كفاءة وفعالية المطحنة الكروية إلى أقصى حد، مما يضمن نتائج طحن عالية الجودة لمجموعة واسعة من المواد.
جدول ملخص:
العامل الرئيسي | الوصف |
---|---|
مبادئ التشغيل | يضمن التأثير (قوة التصادم) والتآكل (صقل الجسيمات) الطحن. |
السرعة الحرجة | سرعة الدوران المثلى للكرات لطحن المواد بفعالية. |
أبعاد الأسطوانة | نسبة الطول: D من 1.56-1.64 تضمن طحنًا متوازنًا. |
وسائط الطحن (الكرات) | يؤثر الحجم والكثافة ونسبة الملء على كفاءة الطحن. |
خصائص المواد | تؤثر الصلابة والكثافة ومحتوى الرطوبة على طاقة الطحن والوقت. |
عوامل التشغيل | تحدد سرعة الدوران وزمن المكوث ومعدل التغذية فعالية الطحن. |
إزالة المنتج في الوقت المناسب | يضمن الطحن المستمر ويمنع الطحن الزائد أو الانسداد. |
حسِّن عملية الطحن الخاصة بك مع رؤى الخبراء- اتصل بنا اليوم للحصول على حلول مصممة خصيصاً لك!