تُعد عملية خلط مركبات المطاط خطوة حاسمة في تصنيع المطاط، حيث يتم تحويل المواد الخام إلى مركب مطاطي موحد. ويتضمن ذلك خلط المكونات وتليينها وتجانسها وتشتيتها من خلال قوى القص الميكانيكية والحرارة. تضمن العملية التلامس الشامل والتشتت المنتظم لعوامل التركيب داخل مصفوفة المطاط. وتلعب المعدات الرئيسية مثل الخلاطات الداخلية، مع دواراتها الدوارة، دورًا حيويًا في تحقيق الخلط الفعال من خلال قص وفرك المواد، وتقليل اللزوجة، وتعزيز قابلية التبلل. ثم تتم معالجة المركب المخلوط بعد ذلك من خلال طرق مثل البثق والتقويم والفلكنة لإنتاج منتجات مطاطية تامة الصنع.
شرح النقاط الرئيسية:
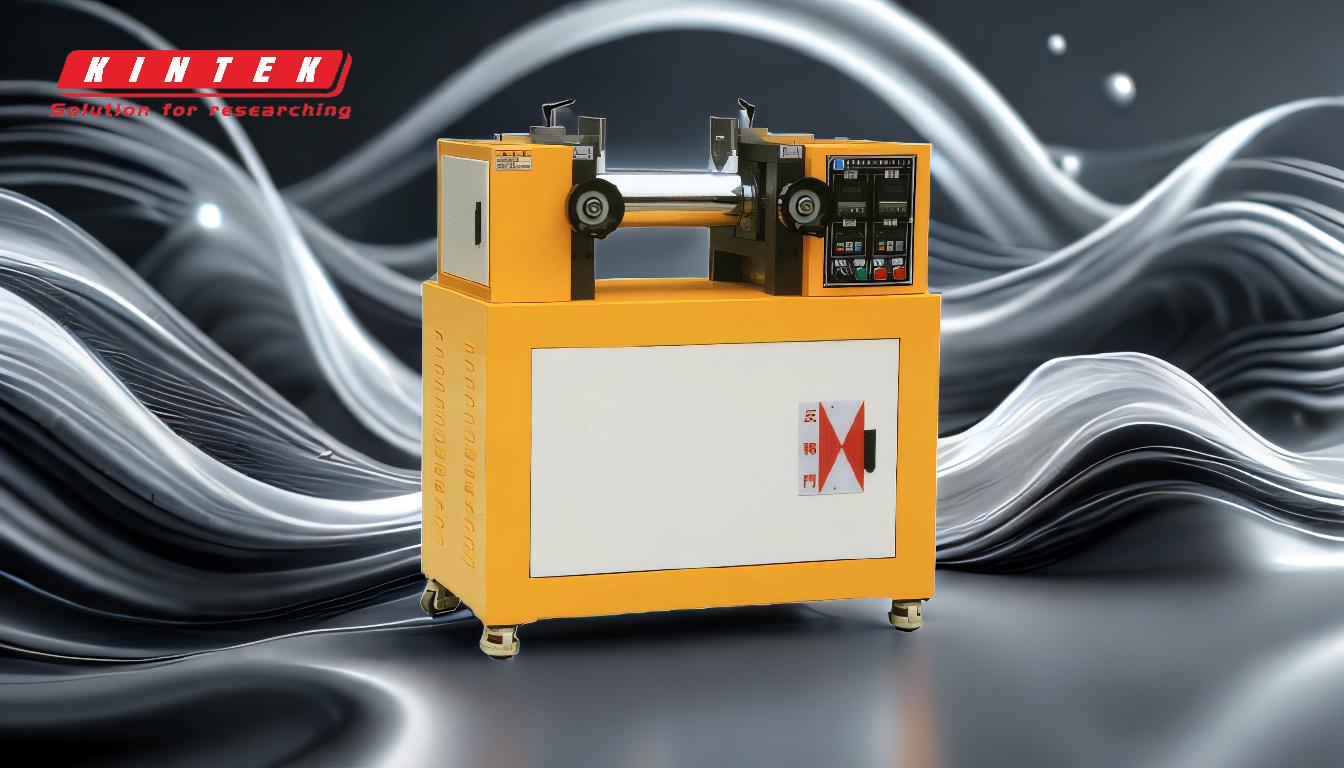
-
الغرض من خلط المطاط:
- خلط المطاط هو عملية الجمع بين المواد الخام (مثل المطاط الطبيعي والمطاط الصناعي والمواد المالئة والملدنات وعوامل المعالجة) لإنشاء مركب مطاطي متجانس.
- والهدف من ذلك هو تحقيق تشتت موحد لجميع المكونات، مما يضمن خصائص متسقة في المنتج النهائي.
-
قوى القص الميكانيكية والحرارة:
- تعتمد عملية الخلط على قوى القص الميكانيكية، والتي يتم توليدها بواسطة معدات مثل الخلاطات الداخلية.
- أثناء دوران الدوارات، فإنها تقوم بقص المواد المطاطية وفركها، مما يولد حرارة. وتقلل هذه الحرارة من لزوجة المطاط، مما يسهل خلط وتشتيت عوامل التركيب.
-
دور الخلاطات الداخلية:
- تُستخدم الخلاطات الداخلية بشكل شائع لخلط المطاط. وهي تتكون من اثنين من الدوارات التي تدور بالنسبة لبعضها البعض، مما يخلق قوى القص.
- تقوم النتوءات الموجودة على الدوارات بتقليب وقص المادة باستمرار، مما يضمن الخلط الشامل والتشتت المنتظم للمواد المضافة.
- تعمل الحرارة المتولدة أثناء الخلط أيضًا على تحسين قابلية تبلل المطاط على سطح عامل التركيب، مما يعزز التلامس والتشتت.
-
الخطوات الرئيسية في عملية الخلط:
- الخلط: يتم دمج المواد الخام بنسب محددة لإنشاء مركب المطاط المطلوب.
- التليين: تعمل قوى القص الميكانيكية والحرارة على تليين المطاط، مما يجعله أكثر مرونة وأسهل في الخلط.
- التجانس: تتم معالجة الخليط حتى يحصل على قوام متجانس.
- التشتيت: يتم توزيع عوامل التركيب (مثل الحشوات وعوامل المعالجة) بالتساوي في جميع أنحاء مصفوفة المطاط.
-
التحديات في الخلط:
- يميل المطاط الطبيعي (NR) إلى الزيادة في اللزوجة أثناء التخزين الطويل، مما قد يؤدي إلى تعقيد عملية الخلط. قد تكون المعالجة المسبقة أو التكييف مطلوبة لمعالجة هذه المشكلة.
- قد يكون تحقيق التشتت المنتظم للمواد المضافة، خاصةً في المركبات عالية اللزوجة، أمرًا صعبًا ويتطلب تحكمًا دقيقًا في معاملات الخلط.
-
عمليات ما بعد الخلط:
-
بعد الخلط، يخضع المركب المطاطي لعمليات إضافية لتشكيله ومعالجته في المنتجات النهائية. وتشمل هذه العمليات:
- البثق: تشكيل المطاط إلى مقاطع أو صفائح متصلة.
- التقويم: دحرجة المطاط إلى صفائح رقيقة أو أقمشة طلاء باستخدام تقويم المطاط .
- الفلكنة: معالجة المطاط لتحسين قوته ومرونته ومتانته من خلال الربط الكيميائي باستخدام مبركن المطاط .
-
بعد الخلط، يخضع المركب المطاطي لعمليات إضافية لتشكيله ومعالجته في المنتجات النهائية. وتشمل هذه العمليات:
-
أهمية التحكم في درجة الحرارة:
- تلعب درجة الحرارة دورًا حاسمًا في عملية الخلط. فالحرارة المفرطة يمكن أن تؤدي إلى تدهور المطاط، في حين أن الحرارة غير الكافية قد تعيق التشتت السليم للمواد المضافة.
- غالبًا ما تشتمل الخلاطات الحديثة على أنظمة تبريد لتنظيم درجة الحرارة ومنع ارتفاع درجة الحرارة.
-
ضمان الجودة:
- يتم تقييم جودة مركب المطاط المخلوط من خلال اختبارات التوحيد والتشتت والخصائص الميكانيكية.
- ويضمن الخلط المتسق أن المنتج النهائي يفي بالمواصفات المطلوبة من حيث القوة والمرونة وخصائص الأداء الأخرى.
من خلال فهم هذه النقاط الرئيسية، يمكن للمشترين والمصنعين ضمان تحسين عملية خلط المطاط من أجل الجودة والكفاءة والاتساق في إنتاج مركبات مطاطية عالية الأداء.
جدول ملخص:
الجوانب الرئيسية | التفاصيل |
---|---|
الغرض | الجمع بين المواد الخام لإنتاج مركب مطاطي متجانس. |
المعدات الرئيسية | خلاطات داخلية ذات دوارات دوارة للقص والخلط الفعال. |
خطوات الخلط | مزج المكونات وتليينها وتجانسها وتشتيتها. |
التحديات | تغيرات اللزوجة في المطاط الطبيعي، والتشتت المنتظم للمواد المضافة. |
عمليات ما بعد الخلط | البثق والتقويم والفلكنة للتشكيل والمعالجة. |
التحكم في درجة الحرارة | ضروري لمنع التدهور وضمان التشتت السليم للمواد المضافة. |
ضمان الجودة | اختبارات التوحيد والتشتت والخصائص الميكانيكية. |
حسِّن عملية خلط المطاط من أجل الجودة والكفاءة- اتصل بخبرائنا اليوم !