تصلب السطح هو عملية تستخدم لزيادة صلابة السطح الخارجي للمعدن مع الحفاظ على قلب أكثر ليونة وأكثر ليونة. تعتبر هذه التقنية ضرورية لتحسين مقاومة التآكل وقوة الكلال والمتانة الشاملة للمكونات. يتم استخدام طرق ومنتجات مختلفة لتصلب الأسطح، بما في ذلك المعالجة الحرارية والمعالجات الكيميائية والعمليات الميكانيكية. يعتمد اختيار الطريقة على المادة والتطبيق والخصائص المطلوبة.
وأوضح النقاط الرئيسية:
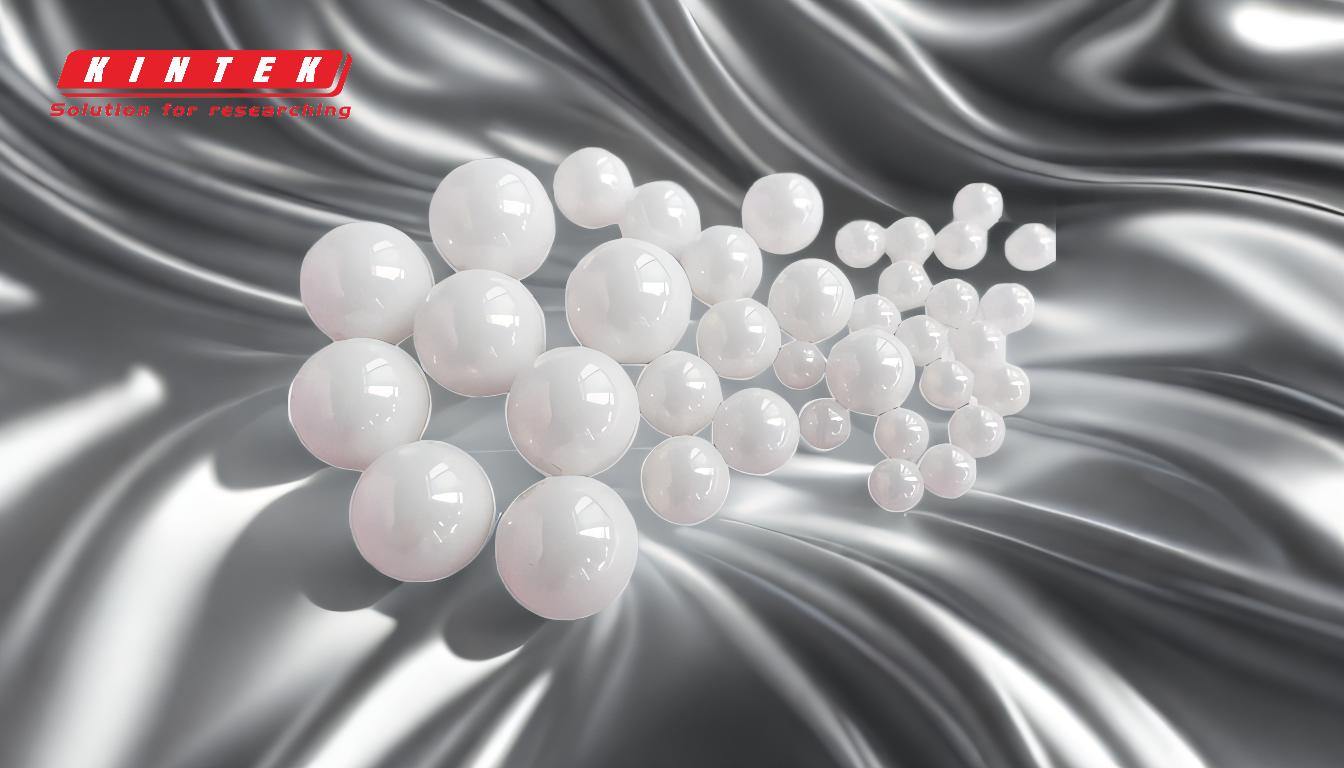
-
طرق المعالجة الحرارية:
- تصلب الحث: تستخدم هذه الطريقة الحث الكهرومغناطيسي لتسخين سطح المعدن، يليه التبريد السريع. يتم استخدامه بشكل شائع للتروس والأعمدة والمكونات الأخرى التي تتطلب صلابة سطحية عالية.
- تصلب اللهب: يتضمن ذلك تسخين السطح المعدني بلهب أوكسي أسيتيلين ثم إخماده. إنها مناسبة للمكونات الكبيرة والأشكال غير المنتظمة.
- تصلب الليزر: يتم استخدام شعاع الليزر المركز لتسخين السطح، يليه التبريد الذاتي بسبب تبديد الحرارة السريع في المادة السائبة. توفر هذه الطريقة الدقة والحد الأدنى من التشويه.
-
طرق المعالجة الكيميائية:
- الكربنة: تتضمن هذه العملية إدخال الكربون إلى الطبقة السطحية للصلب منخفض الكربون عن طريق تسخينه في بيئة غنية بالكربون. ينتشر الكربون إلى السطح، مما يزيد من صلابته بعد التبريد.
- نيترة: تقوم هذه الطريقة بإدخال النيتروجين إلى سطح المعدن، مما يؤدي إلى تكوين نيتريدات صلبة. يتم تنفيذه في درجات حرارة منخفضة، مما يقلل من التشوه ويجعله مناسبًا للمكونات النهائية.
- السيانيد: عملية يتم فيها تسخين المعدن في حمام السيانيد المنصهر، مما يسمح للكربون والنيتروجين بالانتشار في السطح. وهو أقل استخدامًا بسبب المخاوف البيئية.
-
الطرق الميكانيكية:
- تسديدة بينينغ: يتضمن ذلك قصف السطح بوسائط كروية صغيرة (طلقات) لتحفيز ضغوط الضغط، مما يؤدي إلى تحسين مقاومة الكلال وصلابة السطح.
- تلميع الأسطوانة: عملية عمل على البارد حيث يتم ضغط أسطوانة صلبة على السطح لتنعيمه وتقويته. غالبًا ما يستخدم لتحسين تشطيب السطح وصلابة المكونات الأسطوانية.
-
المنتجات والمواد:
- الفولاذ: درجات مختلفة من الفولاذ، مثل الفولاذ منخفض الكربون، وسبائك الفولاذ، وفولاذ الأدوات، يتم عادةً تصليب سطحها باستخدام الطرق المذكورة أعلاه.
- الحديد الزهر: يمكن أيضًا تقوية سطح أنواع معينة من الحديد الزهر، مثل حديد الدكتايل، لتحسين مقاومة التآكل.
- السبائك غير الحديدية: يمكن أن تخضع بعض السبائك غير الحديدية، مثل التيتانيوم والألمنيوم، لعمليات تصلب السطح مثل النيترة أو الأنودة لتعزيز خصائص السطح.
-
التطبيقات:
- صناعة السيارات: غالبًا ما تخضع المكونات مثل التروس والأعمدة المرفقية وأعمدة الكامات إلى تصلب السطح لتحمل الضغط العالي والتآكل.
- صناعة الطيران: يتم تقوية سطح الأجزاء المهمة مثل معدات الهبوط وشفرات التوربينات لضمان المتانة والسلامة.
- الأدوات والآلات: يتم تقوية سطح أدوات القطع والقوالب والقوالب لإطالة عمر الخدمة والحفاظ على الدقة.
-
مزايا تصلب السطح:
- تعزيز مقاومة التآكل: السطح الصلب يقاوم التآكل والتآكل، مما يطيل عمر المكون.
- تحسين قوة التعب: تصلب السطح يقدم ضغوطًا ضاغطة تعمل على تحسين مقاومة فشل الكلال.
- قلب الدكتايل: يحافظ القلب الناعم على المتانة والليونة، ويمنع الكسر الهش.
-
اعتبارات الاختيار:
- توافق المواد: ليست كل المواد مناسبة لكل طرق تصلب الأسطح. يعتمد الاختيار على المادة الأساسية وخصائصها.
- هندسة المكونات: يؤثر شكل وحجم المكون على اختيار طريقة التصلب. قد تتطلب الأشكال الهندسية المعقدة طرقًا أكثر دقة مثل التصلب بالليزر.
- التكلفة والكفاءة: بعض الطرق، مثل التقوية بالحث، تكون فعالة من حيث التكلفة لإنتاج كميات كبيرة، بينما البعض الآخر، مثل التقسية بالليزر، قد تكون أكثر تكلفة ولكنها توفر دقة أكبر.
في الختام، تصلب السطح يشمل مجموعة متنوعة من الأساليب والمنتجات المصممة لتعزيز الخصائص السطحية للمعادن. يعتمد اختيار الطريقة المناسبة على المادة والتطبيق والنتائج المرجوة، مما يضمن قدرة المكونات على تحمل متطلبات بيئتها التشغيلية.
جدول ملخص:
فئة | طرق / أمثلة |
---|---|
المعالجة الحرارية | تصلب الحث، تصلب اللهب، تصلب الليزر |
المعالجة الكيميائية | الكربنة، النيترة، السيانيد |
الطرق الميكانيكية | طلقة Peening ، تلميع الأسطوانة |
مواد | الفولاذ، الحديد الزهر، السبائك غير الحديدية |
التطبيقات | السيارات والفضاء والأدوات والآلات |
المزايا | تعزيز مقاومة التآكل، تحسين قوة التعب، الأساسية ليونة |
عوامل الاختيار | توافق المواد وهندسة المكونات والتكلفة والكفاءة |
اكتشف أفضل حلول تصلب الأسطح التي تناسب احتياجاتك — اتصل بخبرائنا اليوم !