يتم تطبيق طلاء الكربون الشبيه بالماس (DLC) باستخدام تقنيات ترسيب متقدمة تضمن الحصول على طلاء قوي ومتين وعالي الأداء. تشمل الطرق الأكثر شيوعًا الترسيب الفيزيائي للبخار (PVD) والترسيب الكيميائي للبخار (CVD)، مع وجود أشكال مختلفة مثل الترسيب الفيزيائي للبخار بمساعدة البلازما بالترددات الراديوية (RF PECVD) والترسيب الكيميائي للبخار بالفتيل الساخن. تتضمن هذه الطرق إنشاء بيئة محكومة في غرفة مفرغة من الهواء، حيث يتم تنشيط ذرات الكربون وترسيبها على الركيزة. يعتمد اختيار الطريقة على مادة الركيزة وخصائص الطلاء المطلوبة ومتطلبات التطبيق. عادةً ما تكون طلاءات DLC رقيقة (0.5 إلى 2.5 ميكرون) وتوفر مقاومة ممتازة للتآكل، واحتكاكًا منخفضًا، ومتانة معززة.
شرح النقاط الرئيسية:
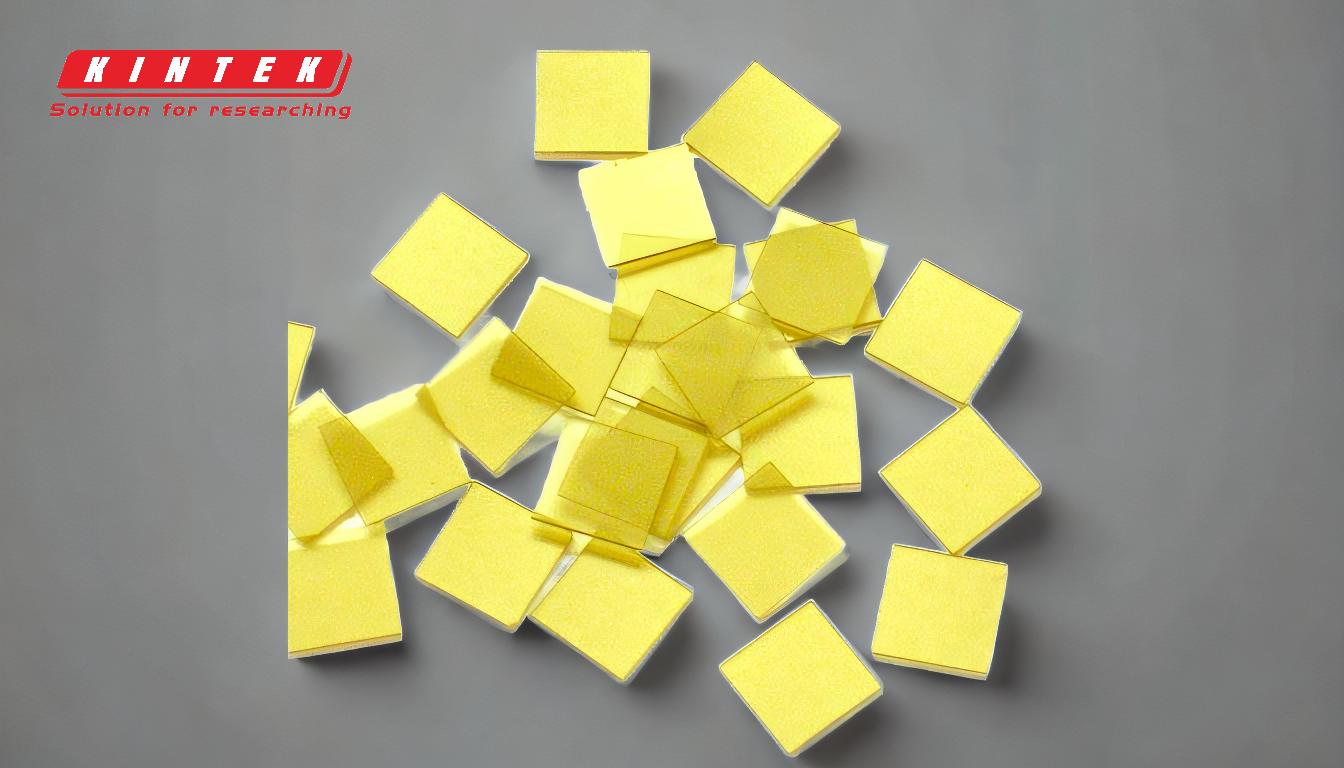
-
نظرة عامة على تطبيق طلاء DLC
- يتم تطبيق طلاءات DLC باستخدام تقنيات ترسيب متقدمة لإنشاء طبقة رقيقة ومتينة من الكربون مع نسبة كبيرة من الروابط sp3.
- يتم تصميم عملية الطلاء بما يتناسب مع مادة الركيزة والاستخدام المقصود، مما يضمن الأداء الأمثل.
-
طرق الترسيب الشائعة
-
الترسيب الفيزيائي للبخار (PVD):
- تتضمن تبخير مادة مصدرية والسماح لها بالتكثف على الركيزة.
- مناسبة لتطبيق طلاءات DLC على أدوات الكربيد، بسُمك نموذجي يتراوح بين 0.5 و2.5 ميكرون.
- تشمل المزايا التحكم الدقيق في سُمك الطلاء وتوحيده.
-
ترسيب البخار الكيميائي (CVD):
- ينطوي على ترسيب ذرات الكربون من المرحلة الغازية (مثل الهيدروجين والميثان) على الركيزة.
- وتتضمن التقنيات الشائعة الترسيب الكيميائي بالبخار الكيميائي (CVD) ذات الفتيل الساخن، والترسيب الكيميائي بالبخار الكيميائي بمساعدة البلازما بالترددات الراديوية (RF PECVD)، والترسيب الكيميائي بالبلازما بالموجات الدقيقة (MPCVD).
- وتتطلب درجات حرارة عالية (أكثر من 750 درجة مئوية) لتنشيط جزيئات الغاز وتشكيل طبقة من الماس.
-
الترسيب الفيزيائي للبخار (PVD):
-
عملية خطوة بخطوة للطلاء بالتقنية CVD
-
التحضير:
- يتم تنظيف الركيزة (على سبيل المثال، أدوات كربيد التنجستن) وتحضيرها لضمان الالتصاق المناسب للطلاء.
-
التحميل في الغرفة:
- يتم وضع الأدوات المحضرة في غرفة تفريغ تحتوي على غازات الهيدروجين والميثان.
-
تنشيط جزيئات الغاز:
- توفر أسلاك التنغستن التي يتم تسخينها إلى أكثر من 2,300 درجة مئوية الطاقة اللازمة لتفتيت جزيئات الغاز وتسخين الأدوات إلى أكثر من 750 درجة مئوية.
-
ترسيب ذرات الكربون:
- إعادة تجميع ذرات الكربون المنشط على سطح الأداة لتشكيل طبقة ماسية نقية.
-
التبريد والإزالة:
- بعد عملية الترسيب، يتم تبريد الأدوات وإزالتها من الحجرة لتكون جاهزة للاستخدام.
-
التحضير:
-
مزايا الطرق المختلفة
-
PVD:
- انخفاض درجات حرارة المعالجة، مما يجعلها مناسبة للركائز الحساسة لدرجات الحرارة.
- دقة عالية وتوحيد في سماكة الطلاء.
-
CVD:
- تنتج أغشية ماسية نقية عالية الجودة وذات التصاق ممتاز.
- مثالية للتطبيقات ذات درجات الحرارة العالية والركائز التي يمكنها تحمل الظروف القاسية.
-
PVD:
-
تطبيقات طلاءات DLC
-
أدوات القطع:
- يعزز مقاومة التآكل ويطيل عمر الأداة.
-
مكونات السيارات:
- يقلل الاحتكاك ويحسّن كفاءة استهلاك الوقود في أجزاء المحرك.
-
الأجهزة الطبية:
- يوفر التوافق الحيوي ومقاومة التآكل للأدوات الجراحية.
-
الإلكترونيات:
- يحسن متانة وأداء المكونات مثل محركات الأقراص الصلبة وأجهزة الاستشعار.
-
أدوات القطع:
-
اعتبارات لمشتري المعدات والمواد الاستهلاكية
-
توافق الركيزة:
- التأكد من توافق الطريقة المختارة مع مادة الركيزة (مثل الكربيد أو الفولاذ أو السيراميك).
-
سمك الطلاء والتوحيد:
- تقييم السماكة والتوحيد المطلوبين للتطبيق المحدد.
-
التكلفة وقابلية التوسع:
- النظر في فعالية التكلفة وقابلية التوسع للطريقة المختارة للإنتاج على نطاق واسع.
-
العوامل البيئية وعوامل السلامة:
- تقييم التأثير البيئي ومتطلبات السلامة لعملية الترسيب.
-
توافق الركيزة:
من خلال فهم هذه النقاط الرئيسية، يمكن لمشتري المعدات والمواد الاستهلاكية اتخاذ قرارات مستنيرة بشأن أفضل طريقة طلاء DLC لاحتياجاتهم الخاصة، مما يضمن الأداء الأمثل والفعالية من حيث التكلفة.
جدول ملخص:
الجانب | التفاصيل |
---|---|
الطرق الشائعة | PVD، CVD (PECVD بالترددات اللاسلكية PECVD، CVD بالفتيل الساخن) |
سُمك الطلاء | 0.5 إلى 2.5 ميكرون |
المزايا الرئيسية | مقاومة التآكل، وانخفاض الاحتكاك، والمتانة |
التطبيقات | أدوات القطع، وقطع غيار السيارات، والأجهزة الطبية، والإلكترونيات |
توافق الركيزة | الكربيد والفولاذ والسيراميك |
نطاق درجة الحرارة | PVD: درجات حرارة منخفضة؛ CVD: أكثر من 750 درجة مئوية |
العوامل البيئية | غرفة تفريغ، بيئة غازية خاضعة للتحكم |
اكتشف حل طلاء DLC المثالي لاحتياجاتك- اكتشف حل طلاء DLC المثالي لاحتياجاتك- اتصل بخبرائنا اليوم !