اللحام بالنحاس في الفرن هو عملية دقيقة ومضبوطة تُستخدم لربط المكونات المعدنية عن طريق صهر معدن حشو (سبيكة لحام بالنحاس) في الوصلة دون صهر المعادن الأساسية.يتم إجراؤها عادةً في فرن لحام نحاسي مفرغ من الهواء لضمان بيئة نظيفة خالية من الأكسيد، وهو أمر بالغ الأهمية لتحقيق وصلات قوية وموثوقة.وتتضمن العملية عدة خطوات رئيسية، بما في ذلك تنظيف الأجزاء وتحضيرها، والتجميع والتركيب، والتسخين في بيئة خاضعة للتحكم، ومعالجات ما بعد التفريغ.تلغي بيئة التفريغ الحاجة إلى التدفق، وتمنع الأكسدة، وتضمن نتائج عالية الجودة، خاصةً بالنسبة لمواد مثل الفولاذ المقاوم للصدأ والتيتانيوم والسبائك الفائقة.
شرح النقاط الرئيسية:
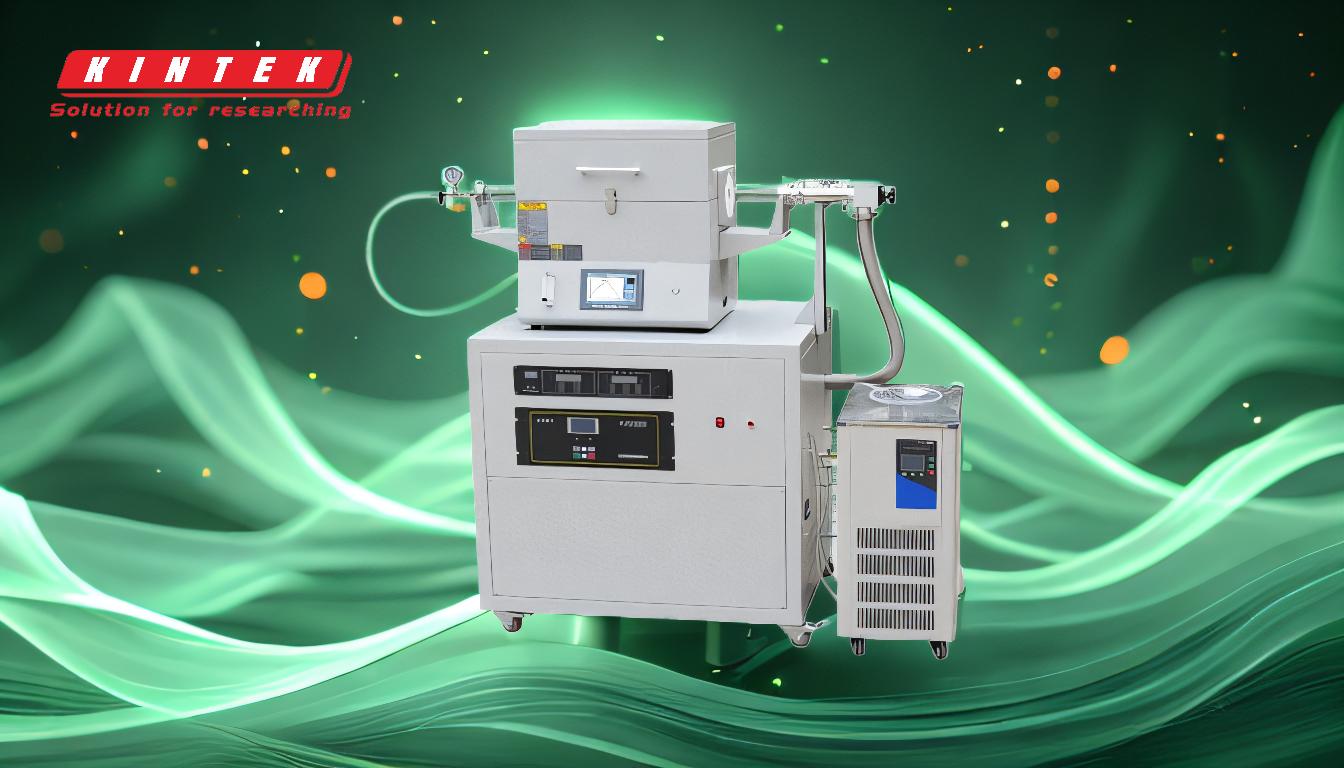
-
تنظيف الأجزاء وتحضيرها
- قبل اللحام بالنحاس، يجب تنظيف الأسطح المعدنية جيدًا لإزالة الملوثات مثل الزيوت والشحوم والأكاسيد.
- تشمل طرق التنظيف التنظيف بالموجات فوق الصوتية أو إزالة الشحوم بالبخار أو الحفر الكيميائي.
- يضمن التنظيف السليم ترطيب وتدفق مثالي لمعدن الحشو، وهو أمر ضروري لتشكيل وصلة قوية.
-
التجميع والتركيب
- يتم تجميع الأجزاء النظيفة وتركيبها للحفاظ على المحاذاة والتباعد الدقيق أثناء عملية اللحام بالنحاس.
- يعد التصميم المناسب للمفصل وعرض الفجوة أمرًا بالغ الأهمية للسماح بحركة الشعيرات الدموية التي تسحب معدن الحشو المنصهر إلى المفصل.
- غالبًا ما تستخدم التركيبات أو المشابك لتثبيت الأجزاء في مكانها ومنع الحركة أثناء التسخين.
-
التسخين في بيئة تفريغ الهواء
- توضع الأجزاء المجمعة في فرن لحام نحاسي مفرغ من الهواء حيث يتم تفريغ الحجرة لإزالة الأكسجين والغازات التفاعلية الأخرى.
- تمنع بيئة التفريغ الأكسدة وتلغي الحاجة إلى التدفق، مما يضمن وصلات نظيفة وعالية الجودة.
- يتم تسخين الفرن إلى درجة حرارة أعلى من درجة انصهار معدن الحشو ولكن أقل من درجة انصهار المعادن الأساسية.
- يتم التحكم في درجة الحرارة بعناية لضمان التسخين المنتظم والصهر المناسب لمعدن الحشو.
-
التبريد والفحص
- بعد عملية اللحام بالنحاس، يتم تبريد الفرن ببطء إلى درجة حرارة الغرفة لتقليل الإجهاد الحراري والتشويه في الأجزاء.
- قد تتضمن عملية التبريد تدوير الغازات الخاملة مثل الأرجون في الغرفة لمنع الأكسدة أثناء التبريد.
- وبمجرد تبريدها، تتم إزالة الأجزاء من الفرن وفحصها للتأكد من جودتها، بما في ذلك سلامة الوصلة وتشطيب السطح.
-
معالجات ما بعد اللحام بالنحاس
- اعتمادًا على التطبيق، يمكن إجراء معالجات ما بعد اللحام بالنحاس، مثل المعالجة الحرارية أو المعالجة الآلية أو تشطيب السطح.
- تعمل هذه المعالجات على تحسين الخواص الميكانيكية ودقة الأبعاد ومظهر المجموعة الملحومة بالنحاس.
-
مزايا التفريغ بالنحاس
- تضمن بيئة التفريغ الحصول على وصلة نظيفة وخالية من الأكسيد، وهو أمر مهم بشكل خاص للمواد المعرضة للأكسدة، مثل الفولاذ المقاوم للصدأ والتيتانيوم والسبائك الفائقة.
- العملية قابلة للتكرار بدرجة كبيرة ومناسبة للتركيبات المعقدة أو الحساسة.
- كما أنها تلغي الحاجة إلى التدفق، مما يقلل من خطر التلوث ويسهّل عملية التنظيف بعد اللحام بالنحاس.
-
تطبيقات اللحام بالنحاس في الفرن
- تُستخدم عملية اللحام بالنحاس في الفرن على نطاق واسع في صناعات مثل الفضاء والسيارات والأجهزة الطبية والإلكترونيات.
- وهو مثالي لربط المكونات التي تتطلب قوة ودقة وموثوقية عالية، مثل المبادلات الحرارية وشفرات التوربينات وأجهزة الاستشعار.
من خلال اتباع هذه الخطوات والاستفادة من إمكانيات فرن اللحام بالنحاس المفرغ من الهواء ، يمكن للمصنعين تحقيق وصلات نحاسية قوية ومتينة وعالية الجودة لمجموعة واسعة من التطبيقات.
جدول ملخص:
الخطوة | الوصف |
---|---|
التنظيف والتحضير | إزالة الملوثات مثل الزيوت والشحوم والأكاسيد باستخدام طرق الموجات فوق الصوتية أو الكيميائية. |
التجميع والتركيب | قم بمحاذاة الأجزاء بدقة واستخدم التركيبات للحفاظ على التباعد بين الأجزاء من أجل العمل الشعري. |
التسخين في التفريغ | التسخين في فرن لحام نحاسي مفرغ من الهواء لمنع الأكسدة وضمان نظافة الوصلات. |
التبريد والفحص | التبريد البطيء لتقليل الإجهاد، وفحص الوصلات للتأكد من سلامتها وتشطيب السطح. |
معالجات ما بعد اللحام بالنحاس | إجراء المعالجة الحرارية أو المعالجة الآلية أو التشطيب لتحسين الخصائص. |
المزايا | وصلات نظيفة وخالية من الأكسيد؛ لا تحتاج إلى تدفق؛ مثالية للمواد المعرضة للأكسدة. |
التطبيقات | صناعات الفضاء والسيارات والأجهزة الطبية والإلكترونيات. |
اكتشف كيف يمكن لحام الأفران بالنحاس الأصفر أن يعزز عملية التصنيع لديك - اتصل بخبرائنا اليوم اتصل بخبرائنا اليوم !