تلبيد البلازما الشرارة الملبدة (SPS) هي تقنية تلبيد متقدمة تستخدم التيار المباشر النبضي (DC) والضغط الأحادي المحور لتوحيد المساحيق بسرعة في مواد سائبة كثيفة ومتجانسة.وتنطوي العملية على تمرير تيار كهربائي عبر قالب موصل (عادةً الجرافيت)، وإذا أمكن، العينة نفسها، مما يولد درجات حرارة عالية موضعية وتفريغ البلازما.وينتج عن ذلك تسخين سريع وتوزيع موحد لدرجات الحرارة وتكثيف فعال في درجات حرارة منخفضة مقارنة بطرق التلبيد التقليدية.تشمل المعلمات الرئيسية معدل التسخين ودرجة حرارة التلبيد والضغط المطبق وخصائص التيار النبضي والغلاف الجوي (التفريغ أو الغاز المتحكم فيه).يتم التحكم في هذه المعلمات بعناية لتحقيق خصائص المواد والبنية المجهرية المثلى.
شرح النقاط الرئيسية:
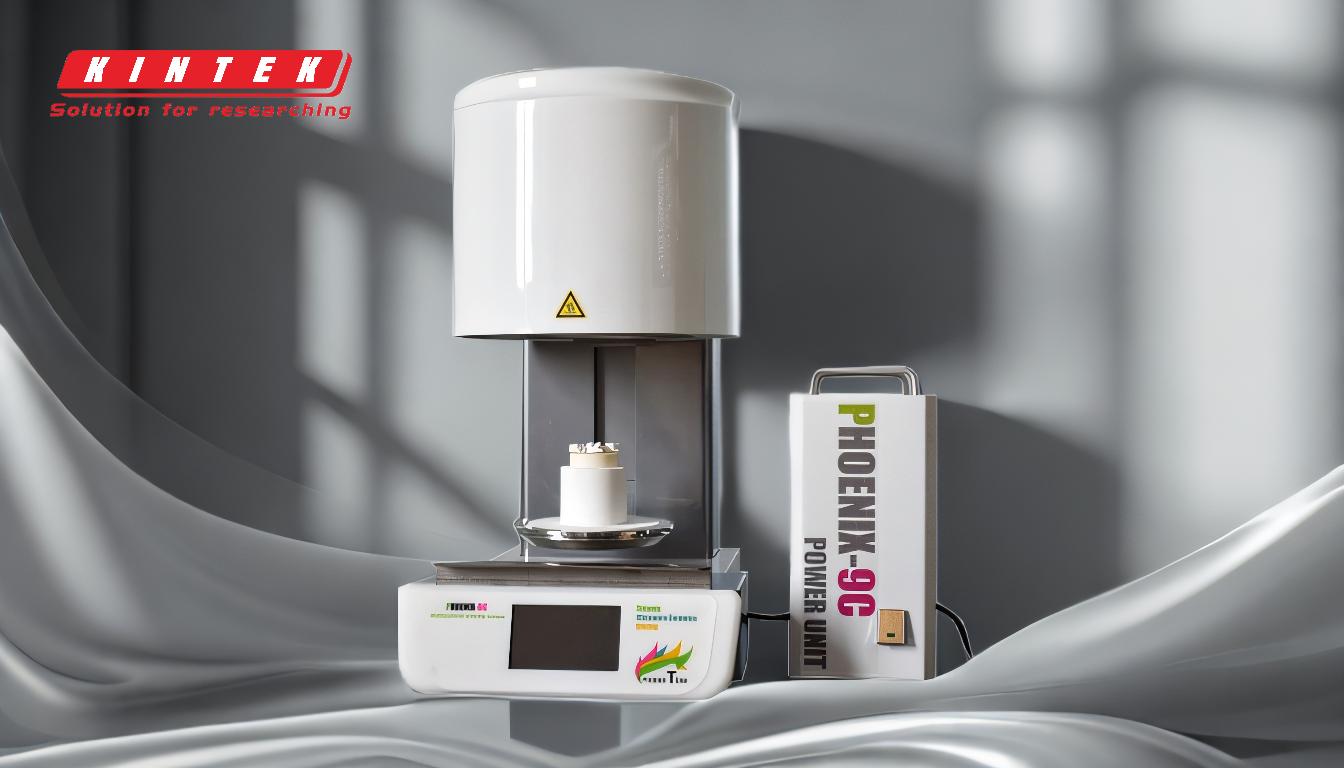
-
معدل التسخين:
- يكون معدل التسخين في SPS أسرع بكثير من طرق التلبيد التقليدية، وغالبًا ما يصل إلى مئات الدرجات في الدقيقة.يقلل هذا التسخين السريع من نمو الحبيبات ويسمح بالاحتفاظ بالبنى المجهرية الدقيقة.
- يتم تحقيق معدلات تسخين عالية من خلال المرور المباشر للتيار عبر القالب والعينة، مما يتيح التسخين الداخلي والخارجي في وقت واحد.
-
درجة حرارة التلبيد:
- يعمل SPS عادةً عند درجات حرارة تلبيد أقل مقارنة بالطرق التقليدية، وغالبًا ما تكون أقل بعدة مئات من الدرجات.ويرجع ذلك إلى التسخين الموضعي وتوليد البلازما في واجهات الجسيمات، مما يعزز الانتشار والترابط.
- يتم التحكم في درجة حرارة التلبيد بدقة لضمان التكثيف الكامل دون نمو مفرط للحبيبات أو تدهور المواد.
-
الضغط المطبق:
- يتم تطبيق الضغط الأحادي المحور أثناء عملية التلبيد للمساعدة في إعادة ترتيب الجسيمات وتشوه اللدونة والتكثيف.يساعد الضغط على إغلاق المسام وتحسين الخواص الميكانيكية للمنتج النهائي.
- وعادة ما يكون الضغط المطبق في نطاق 10-100 ميجا باسكال، اعتمادًا على المادة والخصائص المطلوبة.
-
خصائص تيار النبض:
- يعتبر التيار المستمر النبضي النابض سمة مميزة لـ SPS، حيث يولد تفريغ البلازما بين الجسيمات.وتعزز هذه البلازما الانتشار السطحي وانتشار العيوب الحدودية، مما يعزز التلبيد السريع.
- تعد مدة النبض وتردده وسعته من المعلمات الحرجة التي تؤثر على حركية التلبيد وخصائص المواد النهائية.
-
الغلاف الجوي:
- غالبًا ما يتم إجراء SPS في فراغ أو جو متحكم فيه (على سبيل المثال، غاز خامل) لمنع أكسدة المادة وتلوثها.وهذا مهم بشكل خاص للمواد التفاعلية أو عالية النقاء.
- يضمن الجو المتحكم فيه سلامة المنتج الملبد ويقلل من العيوب.
-
مكونات المعدات:
- يشتمل نظام SPS على جسم الفرن، ونظام الضغط، ونظام التفريغ، ومصدر طاقة التيار المستمر النبضي، ونظام التحكم، وميزات السلامة.يعد قالب الجرافيت ونظام تبريد الماء ضروريين للحفاظ على انتظام درجة الحرارة ومنع ارتفاع درجة الحرارة.
- يسمح التحكم الآلي في البرنامج بالتنظيم الدقيق لدرجة الحرارة والضغط والتيار، مما يضمن التكرار والجودة.
-
مزايا SPS:
- تمكّن معدلات التسخين والتبريد السريعة من إنتاج مواد ذات بنى مجهرية دقيقة وخصائص محسنة.
- تقلل درجات حرارة التلبيد المنخفضة من استهلاك الطاقة وتقلل من الإجهاد الحراري على المواد.
- العملية متعددة الاستخدامات وقابلة للتطبيق على مجموعة واسعة من المواد، بما في ذلك السيراميك والمعادن والمواد المركبة.
-
التطبيقات:
- تُستخدم تقنية SPS على نطاق واسع في الأبحاث والصناعة لتصنيع مواد متقدمة مثل السيراميك النانوي والقطع المعدنية البينية والمواد المتدرجة وظيفياً.
- وتُعد هذه التقنية ذات قيمة خاصة للمواد التي يصعب تلبيدها باستخدام الطرق التقليدية بسبب درجات الانصهار العالية أو الحساسية لنمو الحبيبات.
ومن خلال التحكم الدقيق في هذه البارامترات، تتيح تقنية SPS إنتاج مواد عالية الجودة بخصائص مصممة خصيصًا، مما يجعلها أداة قوية في علوم المواد والهندسة.
جدول ملخص:
المعلمة | الوصف |
---|---|
معدل التسخين | تسخين سريع (مئات الدرجات/الدقيقة) يقلل من نمو الحبيبات. |
درجة حرارة التلبيد | أقل من الطرق التقليدية، مما يضمن التكثيف دون تدهور. |
الضغط المطبق | 10-100 ميجا باسكال يساعد على إعادة ترتيب الجسيمات وتكثيفها. |
التيار النبضي | يولد تفريغ البلازما، مما يعزز الانتشار والترابط. |
الغلاف الجوي | تفريغ الهواء أو الغاز المتحكم فيه يمنع الأكسدة والتلوث. |
المزايا | بنى مجهرية دقيقة، واستخدام أقل للطاقة، وتعدد استخدامات المواد المختلفة. |
التطبيقات | السيراميك متناهي الصغر والسيراميك متعدد المعادن والمواد المتدرجة وظيفياً. |
أطلق العنان لإمكانيات تلبيد سبارك بلازما الشرارة للمواد الخاصة بك- اتصل بخبرائنا اليوم !