إن التلبيد بالضغط الساخن والتلبيد بالبلازما الشرارة (SPS) كلاهما من تقنيات التلبيد المتقدمة المستخدمة لتكثيف المواد المسحوقة إلى أشكال صلبة، ولكنهما يختلفان اختلافًا كبيرًا في آلياتهما وكفاءتهما وتطبيقاتهما.ويعتمد التلبيد بالضغط الساخن على عناصر التسخين الخارجية والضغط لتحقيق التكثيف، بينما تستخدم تقنية التلبيد بالضغط الساخن مزيجًا من تسخين جول والضغط والجهد النبضي للتيار المستمر لتمكين التلبيد الأسرع في درجات حرارة منخفضة.يتميز SPS بشكل خاص بمعدلات التسخين السريع، والقدرة على إنتاج خصائص مواد فريدة من نوعها، وتعدد الاستخدامات عبر مجموعة واسعة من التطبيقات.فيما يلي، يتم شرح الاختلافات الرئيسية بين هاتين الطريقتين بالتفصيل.
شرح النقاط الرئيسية:
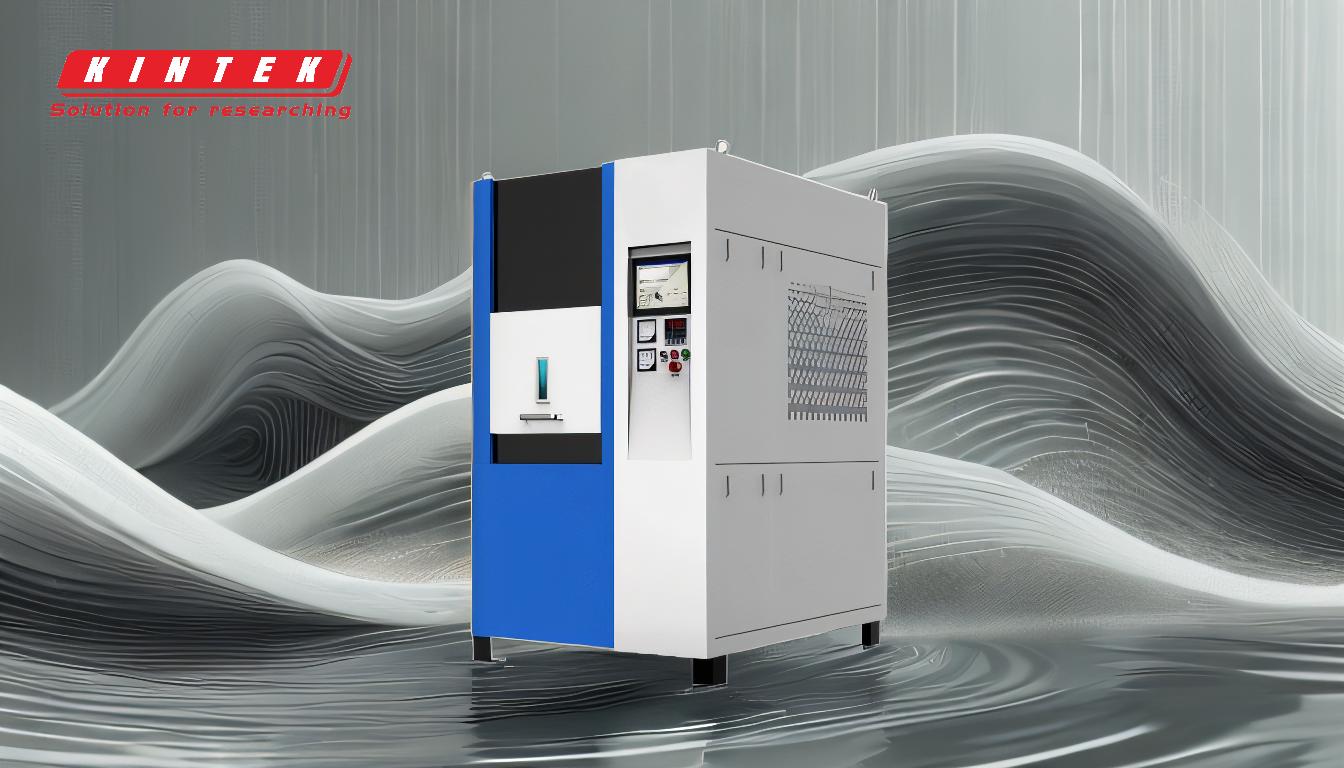
-
آلية التسخين:
- التلبيد بالضغط الساخن:تستخدم الإشعاع من عنصر تسخين خارجي لنقل الحرارة إلى المسحوق المضغوط.هذه العملية أبطأ وتعتمد على التوصيل الحراري من خلال المادة.
- SPS:يولد الحرارة داخليًا من خلال تسخين جولي، حيث يمر تيار كهربائي عبر القالب أو العينة نفسها.وهذا يسمح بمعدلات تسخين عالية للغاية، تصل إلى 1000 درجة مئوية/دقيقة، وهو أسرع بكثير من التلبيد بالضغط الساخن.
-
كفاءة الطاقة:
- التلبيد بالضغط الساخن:يتطلب درجات حرارة أعلى وأوقات تلبيد أطول، مما يؤدي إلى استهلاك طاقة أكبر.
- SPS:تعمل في درجات حرارة أقل وأوقات أقصر بسبب قدرتها على التسخين السريع، مما يجعلها أكثر كفاءة في استهلاك الطاقة.
-
تطبيق الضغط:
- التلبيد بالضغط الساخن:يطبق ضغطًا ثابتًا طوال عملية التلبيد، مما قد يؤدي إلى تكثيف غير متساوٍ في بعض الحالات.
- SPS:يجمع بين الضغط والجهد النبضي للتيار المستمر، مما يعزز تشوه البلاستيك ويعزز التكثيف الأكثر اتساقًا.
-
سرعة التلبيد:
- التلبيد بالضغط الساخن:عادةً ما تكون معدلات التلبيد أبطأ، مما قد يحد من تطبيقه على المواد التي تتطلب معالجة سريعة.
- SPS:يحقق تكثيفًا أسرع من 10 إلى 100 مرة من الطرق التقليدية، مما يجعله مثاليًا للمواد التي تستفيد من التلبيد السريع.
-
خصائص المواد:
- التلبيد بالضغط الساخن:تنتج مواد ذات خواص قياسية، حيث أن العملية محدودة بمعدلات تسخين وتبريد أبطأ.
- SPS:يتيح إنشاء مواد ذات خصائص فريدة من نوعها وربما غير عادية بسبب التسخين والتبريد السريع، والتي يمكن أن تحافظ على البنى المجهرية الدقيقة وتعزز خصائص المواد.
-
تعدد الاستخدامات والتطبيقات:
- التلبيد بالضغط الساخن:مناسبة لمجموعة كبيرة من المواد ولكنها قد لا تكون فعالة مع المواد المتقدمة أو المعقدة.
- SPS:لها نطاق تطبيق أوسع، بما في ذلك المواد النانوية والمركبات والسيراميك المتقدم، نظرًا لقدرتها على التلبيد في درجات حرارة أقل وأوقات أقصر.
-
تعقيد المعدات:
- التلبيد بالضغط الساخن:تستخدم معدات أبسط نسبيًا، مما يجعلها أكثر سهولة لاحتياجات التلبيد التقليدية.
- SPS:تتطلب معدات متخصصة، بما في ذلك مزود طاقة تيار مستمر نابض مما يزيد من تعقيدها وتكلفتها ولكنه يوفر أداءً فائقًا.
من خلال فهم هذه الاختلافات الرئيسية، يمكن لمشتري المعدات والمواد المستهلكة اتخاذ قرارات مستنيرة بشأن طريقة التلبيد التي تناسب المواد ومتطلبات الإنتاج الخاصة بهم.تعتبر SPS، بقدراتها المتقدمة، مفيدة بشكل خاص للتطبيقات المتطورة التي تتطلب معالجة سريعة وخصائص مواد فريدة من نوعها.
جدول ملخص:
الجانب | التلبيد بالضغط الساخن | التلبيد بالبلازما الشرارة (SPS) |
---|---|---|
آلية التسخين | عناصر تسخين خارجية؛ أبطأ، تعتمد على التوصيل الحراري | تسخين جول داخلي؛ معدلات تسخين سريعة (حتى 1000 درجة مئوية/دقيقة) |
كفاءة الطاقة | درجات حرارة أعلى وأوقات تلبيد أطول؛ استهلاك أكبر للطاقة | درجات حرارة أقل وأوقات أقصر؛ كفاءة أكبر في استهلاك الطاقة |
تطبيق الضغط | ضغط ثابت؛ قد يؤدي إلى تكثيف غير متساوٍ | يجمع بين الضغط وجهد التيار المستمر النبضي؛ يعزز التكثيف المنتظم |
سرعة التلبيد | معدلات تلبيد أبطأ؛ محدودة للمعالجة السريعة | 10-100 مرة أسرع من الطرق التقليدية؛ مثالية للتلبيد السريع |
خصائص المواد | خصائص قياسية بسبب معدلات التسخين/التبريد البطيئة | خصائص فريدة واستثنائية؛ تحافظ على البنى المجهرية الدقيقة |
تعدد الاستخدامات | مناسب لمجموعة واسعة من المواد؛ أقل فعالية للمواد المتقدمة/المعقدة | نطاق تطبيق أوسع، بما في ذلك المواد النانوية والمواد المركبة والسيراميك المتقدم |
تعقيد المعدات | معدات أبسط؛ أكثر سهولة لتلبية الاحتياجات التقليدية | معدات متخصصة مزودة بمصدر طاقة تيار مستمر نابض؛ تعقيد وتكلفة أعلى |
هل تحتاج إلى مساعدة في اختيار طريقة التلبيد المناسبة لموادك؟ اتصل بخبرائنا اليوم !