تعد عمليتا VAR (إعادة الصهر بالقوس الهوائي) وESR (إعادة الصهر الكهربائي) عمليتان متميزتان لتكرير الصلب تستخدمان لإنتاج سبائك عالية الجودة مع تحسين الخواص الميكانيكية والنظافة والتجانس. وفي حين أن كلتا العمليتين تهدفان إلى تحسين جودة المواد، إلا أنهما تختلفان اختلافًا كبيرًا في طرقهما ومبادئهما ونتائجهما. تتضمن عملية VAR إعادة صهر قطب كهربائي قابل للاستهلاك تحت التفريغ باستخدام قوس كهربائي، مما يزيل الغازات المذابة والشوائب مع تحقيق التصلب الاتجاهي. وعلى النقيض من ذلك، يستخدم ESR طبقة خبث منصهرة لتنقية القطب الكهربائي، مع التركيز على تحسين نظافة التضمين وتقليل الفصل. فيما يلي، شرح الاختلافات الرئيسية بين فولاذ VAR وESR بالتفصيل.
شرح النقاط الرئيسية:
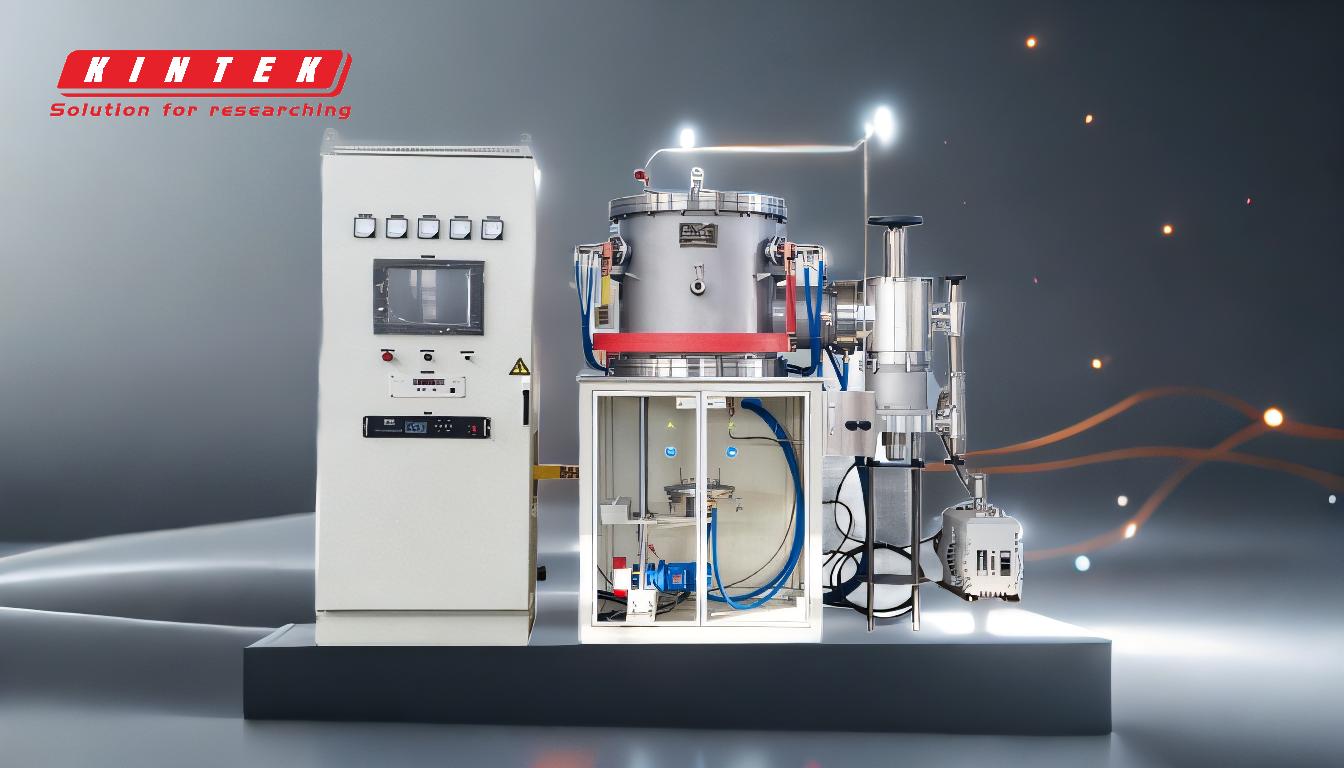
-
آلية العملية:
-
VAR:
- يستخدم قوس كهربائي تحت التفريغ لإعادة صهر قطب كهربائي قابل للاستهلاك.
- يتم صهر القطب بواسطة الحرارة الشديدة للقوس الكهربائي، وتسقط القطرات في قالب مبرد بالماء، مما يشكل سبيكة جديدة.
- تعمل في بيئة عالية التفريغ، مما يساعد على إزالة الغازات الذائبة (مثل الهيدروجين والنيتروجين) والشوائب المتطايرة.
-
ESR:
- يستخدم طبقة خبث منصهرة لصقل القطب الكهربائي.
- يتم صهر القطب عن طريق التسخين بالمقاومة الكهربائية أثناء مروره عبر الخبث الموصل.
- يعمل الخبث كمرشح، حيث يحبس الشوائب والشوائب غير المعدنية، مما يحسن من نظافة الفولاذ.
-
VAR:
-
الظروف البيئية:
-
VAR:
- يتم إجراؤه في فراغ، مما يمنع الأكسدة ويزيل التلوث الجوي.
- مثالية للمعادن التفاعلية مثل التيتانيوم والزركونيوم، وكذلك الفولاذ عالي الأداء والسبائك الفائقة.
-
ESR:
- يتم إجراؤها في جو غاز خامل أو تحت طبقة خبث واقية.
- يوفر الخبث حاجزًا ضد التلوث الجوي، ولكنه لا يوفر نفس مستوى إزالة الغازات الذي يوفره التفريغ.
-
VAR:
-
إزالة الشوائب:
-
VAR:
- تتفوق في إزالة الغازات الذائبة (الهيدروجين والنيتروجين وثاني أكسيد الكربون) والعناصر النزرة المتطايرة.
- تسمح بيئة التفريغ باستخلاص الشوائب ذات الضغط البخاري العالي.
-
ESR:
- يركز على إزالة الشوائب غير المعدنية وتحسين نظافة الأكسيد.
- يلتقط الخبث الشوائب ويحتفظ بها، مما ينتج عنه منتج نهائي أنظف.
-
VAR:
-
التحكم في التصلب:
-
VAR:
- يحقق التصلب الاتجاهي من أسفل إلى أعلى السبيكة.
- يقلل من التجزئة الكلية ويقلل من التجزئة الجزئية، مما يؤدي إلى بنية أكثر تجانسًا.
-
ESR:
- يعزز أيضًا التصلب الاتجاهي ولكنه يعتمد على معدل التبريد وتفاعل الخبث.
- تتأثر عملية التصلب بطبقة الخبث، والتي يمكن أن تؤثر على البنية المجهرية النهائية.
-
VAR:
-
كفاءة الطاقة:
-
VAR:
- معروف بانخفاض مدخلاته من الطاقة مقارنةً بعمليات إعادة الصهر الأخرى.
- تساهم بيئة التفريغ والتسخين القوسي المتحكم فيه في كفاءة الطاقة.
-
ESR:
- يتطلب المزيد من الطاقة بسبب الحاجة إلى الحفاظ على طبقة الخبث المنصهر وعملية التسخين بالمقاومة الكهربائية.
-
VAR:
-
التطبيقات:
-
VAR:
- تُستخدم في المقام الأول للمعادن التفاعلية (التيتانيوم والزركونيوم) والسبائك عالية الأداء (السبائك الفائقة، فولاذ الأدوات).
- مثالية للتطبيقات التي تتطلب مواد فائقة النظافة مع الحد الأدنى من المحتوى الغازي.
-
ESR:
- يُستخدم عادةً في الفولاذ عالي الجودة، مثل فولاذ الأدوات، والفولاذ الحامل، والفولاذ المقاوم للصدأ.
- مناسب للاستخدامات التي تكون فيها نظافة التضمين والتجانس أمرًا بالغ الأهمية.
-
VAR:
-
المزايا:
-
VAR:
- يزيل الغازات الذائبة والشوائب المتطايرة.
- يحقق التصلب الاتجاهي لتحسين الخواص الميكانيكية.
- استهلاك منخفض للطاقة وعملية صهر خالية من السيراميك.
-
ESR:
- يحسن نظافة التضمين ويقلل من الفصل.
- يعزز التجانس والخصائص الميكانيكية للصلب.
- فعال في تكرير مجموعة كبيرة من درجات الصلب.
-
VAR:
-
القيود:
-
VAR:
- يقتصر على المواد التي تستفيد من التكرير بالتفريغ.
- ارتفاع المعدات والتكاليف التشغيلية بسبب نظام التفريغ.
-
ESR:
- أقل فعالية في إزالة الغازات الذائبة مقارنةً ب VAR.
- يتطلب تحكم دقيق في تركيبة الخبث ودرجة حرارته.
-
VAR:
وخلاصة القول، إن VAR وESR عمليتان متكاملتان، ولكل منهما نقاط قوة فريدة. ويفضل استخدام تقنية VAR للمعادن التفاعلية والتطبيقات التي تتطلب مواد فائقة النظافة مع الحد الأدنى من محتوى الغاز، بينما يفضل استخدام ESR لتحسين نظافة التضمين والتجانس في الفولاذ عالي الجودة. ويعتمد الاختيار بين الاثنين على متطلبات المواد المحددة والخصائص المطلوبة.
جدول ملخص:
أسبكت | VAR (إعادة الصهر بالقوس الهوائي) | إعادة الصهر الكهربائي (ESR) |
---|---|---|
آلية العملية | يستخدم قوس كهربائي تحت التفريغ لإعادة صهر قطب كهربائي قابل للاستهلاك. | يستخدم طبقة خبث منصهرة لصقل القطب الكهربائي عن طريق التسخين بالمقاومة الكهربائية. |
الظروف البيئية | يتم إجراؤها في الفراغ، وهي مثالية للمعادن التفاعلية مثل التيتانيوم والزركونيوم. | يتم إجراؤها في جو غاز خامل أو تحت طبقة خبث واقية. |
إزالة الشوائب | تتفوق في إزالة الغازات الذائبة (الهيدروجين والنيتروجين) والعناصر النزرة المتطايرة. | يركز على إزالة الشوائب غير المعدنية وتحسين نظافة الأكسيد. |
التحكم في التصلب | يحقق التصلب الاتجاهي ويقلل من التصلب الكلي ويحسن التجانس. | يعزز التصلب الاتجاهي ولكنه يتأثر بتفاعل الخبث. |
كفاءة الطاقة | مدخلات طاقة منخفضة بسبب بيئة التفريغ والتسخين القوسي المتحكم فيه. | يتطلب المزيد من الطاقة للحفاظ على طبقة الخبث المنصهر والتسخين بالمقاومة الكهربائية. |
التطبيقات | المعادن التفاعلية (التيتانيوم، الزركونيوم) والسبائك عالية الأداء (السبائك الفائقة، فولاذ الأدوات). | الفولاذ عالي الجودة (فولاذ الأدوات، فولاذ المحامل، الفولاذ المقاوم للصدأ) الذي يتطلب النظافة. |
المزايا | يزيل الغازات المذابة ويحقق التصلب الاتجاهي واستهلاك منخفض للطاقة. | يحسن نظافة التضمين، ويعزز التجانس، وفعال في تكرير أنواع الفولاذ المختلفة. |
القيود | تقتصر على مواد التكرير بالتفريغ، وارتفاع المعدات والتكاليف التشغيلية. | أقل فعالية في إزالة الغازات الذائبة، وتتطلب تحكمًا دقيقًا في تركيبة الخبث. |
هل تحتاج إلى مساعدة في اختيار عملية تكرير الفولاذ المناسبة لاستخدامك؟ تواصل مع خبرائنا اليوم !