الصلب بالكبس على الساخن هو عملية تصنيع تجمع بين الحرارة والضغط لتشكيل وتكثيف مواد الصلب.وتعد هذه الطريقة مفيدة بشكل خاص لإنشاء مكونات عالية القوة والمتانة بأبعاد دقيقة.وتتضمن العملية تسخين الفولاذ إلى درجة حرارة أقل من درجة انصهاره، وتطبيق ضغط كبير لتشويهه، ثم تبريده لتحقيق الخصائص المطلوبة.ويشيع استخدام الكبس على الساخن في صناعات مثل صناعة السيارات والفضاء وتصنيع الأدوات، حيث تكون المواد عالية الأداء ضرورية.تعمل هذه العملية على تحسين الخواص الميكانيكية للفولاذ، مثل الصلابة ومقاومة التآكل وقوة التعب، مما يجعلها مثالية للتطبيقات الصعبة.
شرح النقاط الرئيسية:
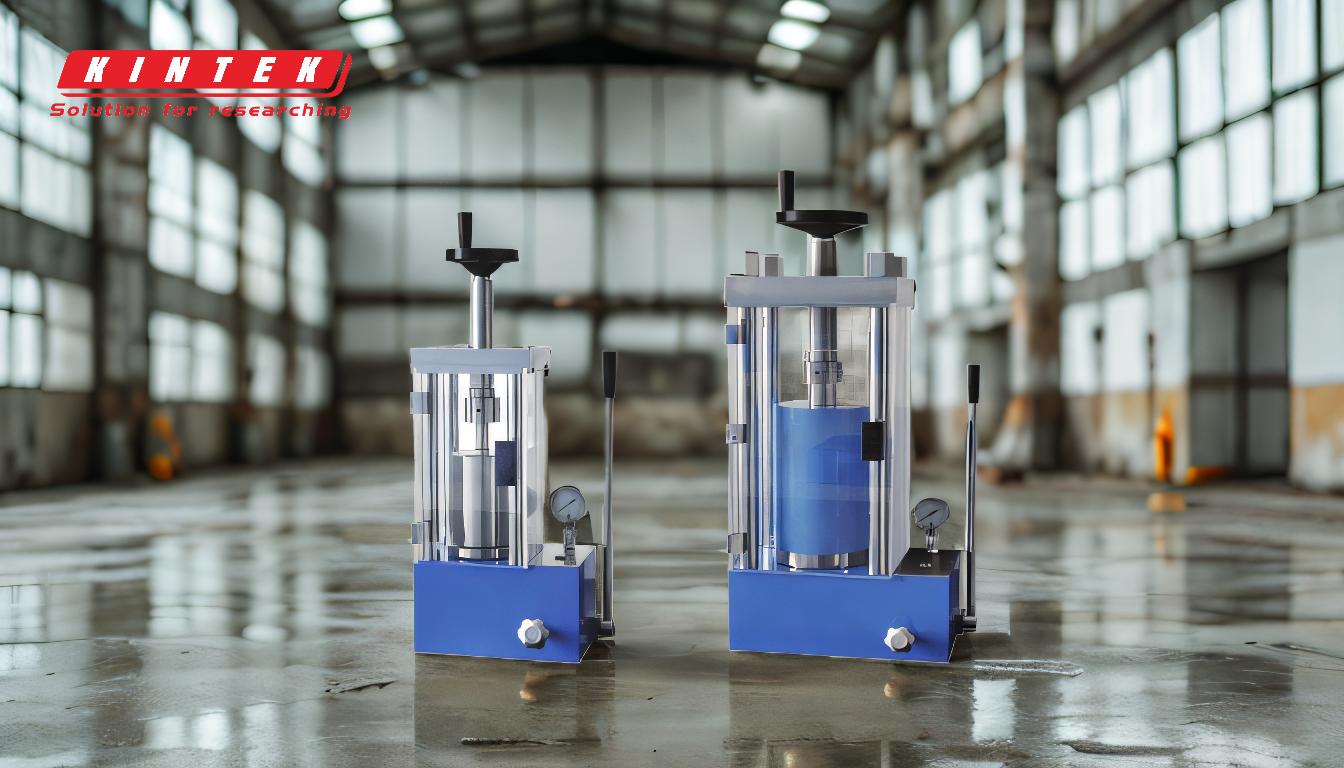
-
تعريف الصلب بالكبس على الساخن والغرض منه:
- الصلب بالضغط الساخن هو تقنية تستخدم الحرارة والضغط لتشكيل وتكثيف مواد الصلب.
- والهدف الأساسي منها هو إنتاج مكونات ذات خواص ميكانيكية محسنة، مثل زيادة الصلابة ومقاومة التآكل وقوة التعب.
- وتعد هذه العملية مفيدة بشكل خاص للتطبيقات التي تتطلب مواد عالية الأداء، كما هو الحال في صناعات السيارات والفضاء.
-
عملية درجة الحرارة والتسخين:
- يتم تسخين الفولاذ إلى درجة حرارة أقل من درجة انصهاره، وعادةً ما تكون في نطاق 800 درجة مئوية إلى 1200 درجة مئوية، اعتمادًا على السبيكة المحددة والخصائص المرغوبة.
- يتم التسخين عادةً في بيئة محكومة، مثل الفرن، لضمان توزيع درجة الحرارة بشكل موحد في جميع أنحاء المادة.
- يجب التحكم في درجة الحرارة بعناية لتجنب ارتفاع درجة الحرارة، مما قد يؤدي إلى تغيرات غير مرغوب فيها في البنية المجهرية أو الذوبان.
-
تطبيق الضغط:
- بمجرد وصول الفولاذ إلى درجة الحرارة المطلوبة، يتم تطبيق ضغط كبير باستخدام مكابس هيدروليكية أو ميكانيكية.
- يساعد الضغط على تشويه الفولاذ، مما يسمح له باتخاذ شكل القالب أو القالب المستخدم في العملية.
- ويعتمد مقدار الضغط المطبق على المتطلبات المحددة للمكون الذي يتم إنتاجه، ولكنه يكون بشكل عام في نطاق 50 إلى 500 ميجا باسكال.
-
التبريد والتصلب:
- بعد عملية الكبس يتم تبريد الفولاذ بمعدل متحكم فيه لتحقيق البنية المجهرية والخصائص الميكانيكية المطلوبة.
- يمكن أن يتم التبريد في الهواء أو الزيت أو الماء، اعتمادًا على السبيكة المحددة والنتيجة المرغوبة.
- يمكن أن يؤدي التبريد السريع (التبريد بالتبريد) إلى زيادة الصلابة، بينما يمكن أن يؤدي التبريد الأبطأ (التلدين) إلى تحسين الليونة وتقليل الضغوط الداخلية.
-
مزايا الصلب بالكبس على الساخن:
- الخواص الميكانيكية المحسنة:يعمل الضغط الساخن على تعزيز قوة الفولاذ وصلابته ومقاومته للتآكل، مما يجعله مناسبًا للتطبيقات عالية الإجهاد.
- الدقة والاتساق:تسمح العملية بإنتاج مكونات ذات أبعاد دقيقة وجودة متسقة.
- كفاءة المواد:يمكن أن يقلل الكبس على الساخن من هدر المواد من خلال تمكين إنتاج مكونات شبه صافية الشكل، والتي تتطلب الحد الأدنى من المعالجة الآلية.
-
تطبيقات الصلب المضغوط على الساخن:
- :: صناعة السيارات:تستخدم لتصنيع التروس والمحامل والمكونات الأخرى عالية الإجهاد.
- صناعة الطيران:مثالية لإنتاج أجزاء خفيفة الوزن وعالية القوة مثل شفرات التوربينات والمكونات الهيكلية.
- تصنيع الأدوات:يشيع استخدامها لصنع أدوات القطع والقوالب والقوالب المتينة.
-
اعتبارات للمشترين:
- اختيار المواد:اختر سبيكة الفولاذ المناسبة بناءً على التطبيق المحدد والخصائص المطلوبة.
- متطلبات المعدات:التأكد من قدرة معدات الكبس الساخن على تحقيق مستويات الحرارة والضغط اللازمة.
- مراقبة الجودة:تنفيذ تدابير صارمة لمراقبة الجودة لضمان اتساق وموثوقية المكونات المضغوطة على الساخن.
من خلال فهم عملية وفوائد الفولاذ المضغوط على الساخن، يمكن للمشترين اتخاذ قرارات مستنيرة عند اختيار المواد والمعدات لتطبيقاتهم المحددة.وتوفر هذه الطريقة طريقة موثوقة لإنتاج مكونات فولاذية عالية الأداء تلبي المتطلبات الصعبة لمختلف الصناعات.
جدول ملخص:
الجانب | التفاصيل |
---|---|
المعالجة | تجمع بين الحرارة والضغط لتشكيل المواد الفولاذية وتكثيفها. |
نطاق درجة الحرارة | 800 درجة مئوية إلى 1200 درجة مئوية، تحت درجة الانصهار. |
نطاق الضغط | من 50 إلى 500 ميجا باسكال، يتم تطبيقه عبر مكابس هيدروليكية أو ميكانيكية. |
طرق التبريد | الهواء أو الزيت أو الماء، حسب الخصائص المرغوبة. |
المزايا الرئيسية | تحسين الصلابة ومقاومة التآكل والدقة وكفاءة المواد. |
التطبيقات | صناعة السيارات، والطيران، والأدوات. |
نصائح للمشتري | اختر السبيكة المناسبة، وتأكد من قدرات المعدات، ونفذ مراقبة الجودة. |
اكتشف كيف يمكن للصلب المضغوط على الساخن أن يعزز عملية التصنيع لديك- اتصل بخبرائنا اليوم !