يعد الغلاف الجوي الخامل أمرًا بالغ الأهمية في مختلف العمليات الصناعية والمعملية والتصنيعية نظرًا لقدرته على منع التفاعلات الكيميائية غير المرغوب فيها وحماية المواد من الأكسدة وتعزيز السلامة من خلال الحد من مخاطر الحريق والانفجارات. من خلال استبدال الغازات التفاعلية مثل الأكسجين بغازات غير تفاعلية مثل النيتروجين أو الأرجون أو ثاني أكسيد الكربون، يضمن الجو الخامل الاستقرار والتحكم في العمليات. وهذا الأمر مهم بشكل خاص في عمليات المعالجة الحرارية وحماية المواد والبيئات التي ترتفع فيها مخاطر التلوث أو الاحتراق. يساعد استخدام الأجواء الخاملة أيضًا في الحفاظ على سلامة المواد والعمليات الحساسة، مما يضمن نتائج متسقة وعالية الجودة.
شرح النقاط الرئيسية:
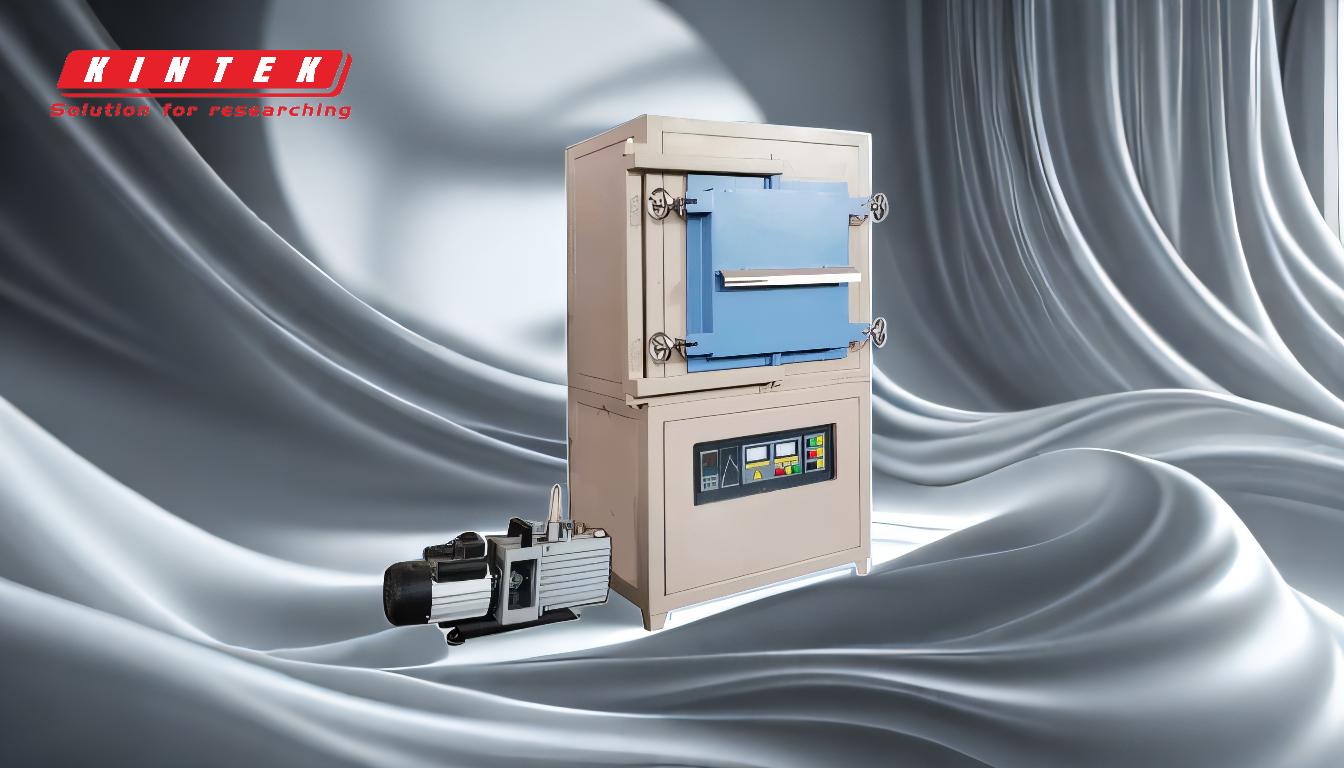
-
منع الحرائق والانفجارات
- تستبدل الأجواء الخاملة الغازات القابلة للاحتراق أو التفاعلية (مثل الأكسجين) بغازات غير تفاعلية مثل النيتروجين أو ثاني أكسيد الكربون.
- وهذا يقلل من خطر الحريق والانفجارات من خلال القضاء على وجود الغازات التي يمكن أن تشتعل أو تتفاعل بشكل متفجر.
- على سبيل المثال، في الصناعات البتروكيماوية أو الصناعات الفضائية، تُستخدم الأجواء الخاملة لمنع الاحتراق العرضي أثناء العمليات ذات درجات الحرارة العالية.
-
الحد من معدلات التفاعل والأكسدة المخفضة
- تتمتع الغازات الخاملة مثل الأرجون والنيتروجين بتفاعلية منخفضة وقدرات أكسدة منخفضة، مما يجعلها مثالية لإبطاء أو منع التفاعلات الكيميائية.
- وهذا أمر بالغ الأهمية في عمليات مثل التلبيد والتلدين الساطع والتلدين بالصلب الساطع وأكسدة الكربون، حيث يمكن أن تؤثر الأكسدة على خصائص المواد.
- من خلال الحفاظ على بيئة مستقرة وغير متفاعلة، تضمن الأجواء الخاملة نتائج متسقة وعالية الجودة في التصنيع.
-
حماية المواد الحساسة
- في المختبرات والأفران الصناعية، تعمل الأجواء الخاملة على حماية العينات والمواد من التلف الناتج عن التعرض للأكسجين أو الرطوبة.
- على سبيل المثال، يتم الحفاظ على المعادن الحساسة أو المركبات التي تتأكسد بسهولة في بيئة خاملة، مما يضمن سلامتها ووظائفها.
- وهذا الأمر مهم بشكل خاص في صناعات مثل الإلكترونيات، حيث يمكن أن يؤثر حتى التلوث البسيط على الأداء.
-
الحفاظ على استقرار العملية
- توفر الأجواء الخاملة بيئة محكومة تظل مستقرة حتى في ظل الظروف المتغيرة، مثل تقلبات درجات الحرارة.
- هذا الثبات ضروري لعمليات مثل المعالجة الحرارية، حيث يضمن التحكم الدقيق في الغلاف الجوي الخصائص المرغوبة للمواد.
- تعتمد صناعات مثل السيارات والفضاء على الأجواء الخاملة لتحقيق نتائج متسقة في التصنيع.
-
الحد من مخاطر التلوث
- تقلل الأجواء الخاملة من خطر التلوث عن طريق منع دخول الغازات أو الجسيمات التفاعلية.
- وهذا أمر حيوي في صناعات مثل المستحضرات الصيدلانية ومعالجة الأغذية، حيث النقاء أمر بالغ الأهمية.
- من خلال إزاحة الأكسجين والغازات التفاعلية الأخرى، تضمن الأجواء الخاملة بقاء المنتجات غير ملوثة وتلبية معايير الجودة.
-
تهيئة ظروف الفراغ
- يمكن استخدام الأجواء الخاملة لخلق ظروف تشبه الفراغ عن طريق إزالة الغازات التفاعلية والحفاظ على بيئة منخفضة الضغط.
- وهذا مفيد في عمليات مثل تصنيع أشباه الموصلات، حيث يمكن حتى للكميات الضئيلة من الأكسجين أن تعطل الإنتاج.
- إن القدرة على التحكم في الغلاف الجوي بدقة تجعل الغازات الخاملة لا غنى عنها في الصناعات عالية التقنية.
-
التطبيقات في عمليات المعالجة الحرارية
- تتطلب عمليات مثل التلبيد والتلدين الساطع والتلدين بالصلب الساطع والتلبيد بالكربون أجواءً عالية التحكم لتحقيق خصائص مواد محددة.
- وتمنع الأجواء الخاملة الأكسدة وغيرها من التفاعلات غير المرغوب فيها أثناء هذه العمليات، مما يضمن البنية المجهرية المطلوبة والسطح النهائي المطلوب.
- وهذا أمر بالغ الأهمية في صناعات مثل صناعة السيارات والفضاء، حيث يرتبط أداء المواد بشكل مباشر بالسلامة والكفاءة.
-
تعزيز السلامة في البيئات الخطرة
- تُستخدم الأجواء الخاملة في البيئات التي توجد فيها غازات أو غبار قابل للاحتراق، مثل المصانع الكيميائية أو مرافق تخزين الحبوب.
- من خلال استبدال الأكسجين بغازات خاملة، ينخفض خطر الاحتراق بشكل كبير، مما يعزز السلامة العامة.
- هذا الإجراء الاستباقي ضروري لمنع الحوادث وحماية العمال والمعدات.
من خلال فهم أهمية الأجواء الخاملة، يمكن للصناعات تحسين عملياتها وتحسين السلامة وضمان جودة وموثوقية منتجاتها. وسواء في التصنيع أو الأبحاث أو البيئات الخطرة، تلعب الأجواء الخاملة دورًا حيويًا في الحفاظ على الاستقرار ومنع التفاعلات غير المرغوب فيها وحماية المواد والأفراد.
جدول ملخص:
الميزة الرئيسية | الوصف |
---|---|
منع الحرائق والانفجارات | استبدال الغازات التفاعلية مثل الأكسجين بغازات خاملة لتقليل مخاطر الاحتراق. |
تقليل الأكسدة المخفضة | يبطئ أو يمنع التفاعلات الكيميائية، مما يضمن سلامة المواد. |
حماية المواد الحساسة | يحمي المواد من التعرض للأكسجين والرطوبة. |
الحفاظ على استقرار العملية | يوفر بيئة مستقرة لتحقيق نتائج متسقة في المعالجة الحرارية. |
الحد من مخاطر التلوث | يضمن نقاء المنتج من خلال منع إدخال الغازات التفاعلية. |
تهيئة ظروف الفراغ | يزيل الغازات التفاعلية للتحكم الدقيق في الصناعات عالية التقنية. |
تطبيقات المعالجة الحرارية | يمنع التأكسد في عمليات التلبيد والتلدين والتلدين بالكربون. |
تعزيز السلامة | يقلل من مخاطر الاحتراق في البيئات الخطرة مثل المصانع الكيميائية. |
تحسين عملياتك باستخدام الغلاف الجوي الخامل- تواصل مع خبرائنا اليوم لمعرفة المزيد!