الكبس على الساخن هو عملية تصنيع تجمع بين الحرارة والضغط لتكثيف وتشكيل المواد، عادةً السيراميك أو المعادن، في هياكل قريبة من الكثافة النظرية.وهي تتضمن وضع المواد المسحوقة في قالب وتطبيق ضغط أحادي المحور (10-30 ميجا باسكال) وتسخينها إلى درجات حرارة التلبيد في وقت واحد.تعمل هذه الطريقة على تسريع التكثيف وتقليل وقت المعالجة وتحسين خصائص المواد مقارنةً بالضغط والتلبيد على البارد التقليدي.وتتضمن العملية خطوات مثل شحن المسحوق، والتنظيف بالمكنسة الكهربائية لإزالة الشوائب، والتسخين لإذابة المسحوق، والضغط لدمج المادة، والتبريد لتصلب المنتج النهائي.يعتبر الكبس الساخن فعالاً بشكل خاص لإنتاج مواد عالية الكثافة وعالية الأداء مع الحد الأدنى من العيوب.
شرح النقاط الرئيسية:
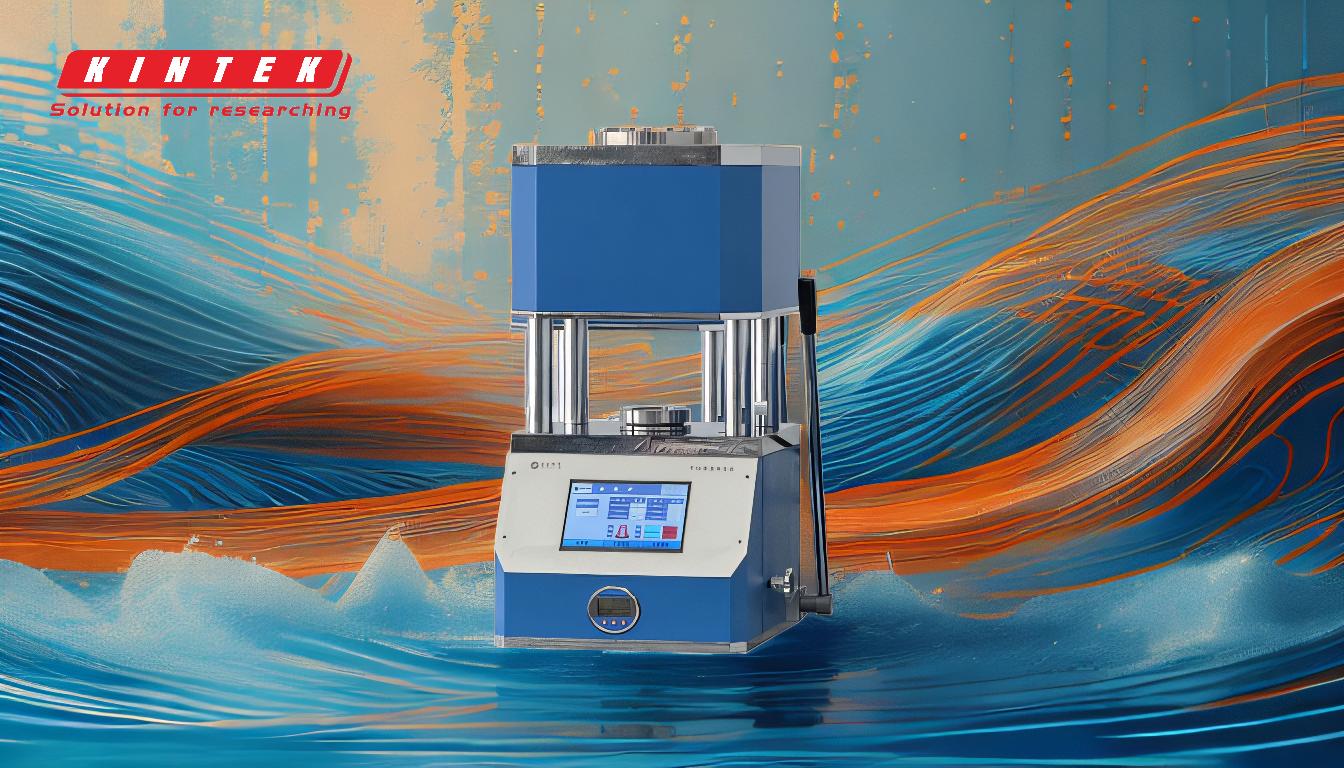
-
التطبيق المتزامن للحرارة والضغط:
- يجمع الكبس الساخن بين الحرارة والضغط في خطوة واحدة، على عكس الطرق التقليدية حيث يكون الكبس والتلبيد عمليتين منفصلتين.يقلل هذا التطبيق المتزامن بشكل كبير من الوقت اللازم لتغيرات الطور وتكوين السبائك.
- تتضمن العملية وضع المواد المسحوقة في قالب جرافيت وتطبيق كل من الحرارة والضغط في نفس الوقت.وهذا يضمن أن تتكثف المادة بشكل موحد وتصل إلى كثافة قريبة من الكثافة النظرية.
-
الضغط أحادي المحور:
- يتم تطبيق ضغط أحادي المحور من 10-30 ميجا باسكال من خلال قالب بسيط الشكل.يساعد هذا الضغط في ضغط المسحوق وزيادة معدل التكثيف.
- يساعد الضغط المطبق في تقليل المسامية وتحسين الخواص الميكانيكية للمنتج النهائي، مما يجعله أكثر كثافة وقوة.
-
الخطوات المتبعة في الكبس على الساخن:
- الشحن:يتم تحميل المسحوق الخزفي أو المعدني في الفرن أو القالب.
- التنظيف بالمكنسة الكهربائية:يتم تفريغ الفرن لخلق فراغ، وإزالة الغازات والشوائب التي يمكن أن تسبب عيوبًا في المنتج النهائي.
- التسخين:يتم رفع درجة الحرارة إلى درجة حرارة التلبيد، مما يذيب جزيئات المسحوق ويسمح لها بالترابط.
- الضغط:يتم تطبيق الضغط لدمج جزيئات المسحوق في بنية كثيفة وصلبة.
- التبريد:يتم تبريد المادة تدريجيًا إلى درجة حرارة الغرفة لتصل إلى درجة حرارة الغرفة لتصلب الهيكل ومنع الإجهاد الحراري.
-
المزايا مقارنة بالطرق التقليدية:
- تقليل وقت المعالجة:من خلال الجمع بين الكبس والتلبيد، يقلل الكبس الساخن بشكل كبير من وقت المعالجة الإجمالي مقارنةً بالكبس والتلبيد البارد التقليدي.
- تحسين خصائص المواد:يؤدي التطبيق المتزامن للحرارة والضغط إلى مواد ذات كثافة أعلى وخصائص ميكانيكية أفضل وعيوب أقل.
- كثافة قريبة من النظرية:يسمح الكبس الساخن للمادة بالوصول إلى كثافات قريبة من الحد الأقصى النظري، وهو أمر يصعب تحقيقه بالطرق الأخرى.
-
التطبيقات:
- يستخدم الكبس الساخن على نطاق واسع في إنتاج السيراميك عالي الأداء والمواد المركبة المتقدمة والمعادن المتخصصة.وهو مفيد بشكل خاص في الصناعات التي تتطلب مواد ذات قوة عالية ومقاومة للتآكل والاستقرار الحراري.
- وتشمل التطبيقات الشائعة مكونات الطيران وأدوات القطع والركائز الإلكترونية.
-
الظروف البيئية:
- يمكن إجراء الكبس على الساخن في فراغ أو تحت ضغط إيجابي من الغاز الخامل.تمنع هذه البيئة الأكسدة والتفاعلات الكيميائية الأخرى التي يمكن أن تؤدي إلى تدهور جودة المادة.
- ويساعد استخدام التفريغ أو الغاز الخامل أيضًا في إزالة أي غازات متبقية أو شوائب من المسحوق، مما يزيد من تحسين جودة المنتج النهائي.
-
اعتبارات المواد:
- يعد اختيار المادة المستخدمة في القالب (الجرافيت عادةً) أمرًا بالغ الأهمية حيث يجب أن تتحمل درجات الحرارة والضغوط العالية دون تشويه أو تفاعل مع المسحوق.
- يجب أن يكون للمسحوق المستخدم توزيع موحد لحجم الجسيمات لضمان التكثيف المتساوي وتجنب العيوب في المنتج النهائي.
من خلال فهم هذه النقاط الرئيسية، يمكن للمرء أن يقدّر كفاءة وفعالية الكبس الساخن في إنتاج مواد عالية الجودة وكثيفة ذات خصائص فائقة.هذه الطريقة مفيدة بشكل خاص للصناعات التي تتطلب مواد ذات أداء ميكانيكي وحراري استثنائي.
جدول ملخص:
الجانب الرئيسي | التفاصيل |
---|---|
المعالجة | تجمع بين الحرارة والضغط لتكثيف السيراميك أو المعادن. |
الضغط | ضغط أحادي المحور من 10-30 ميجا باسكال مطبق. |
الخطوات | الشحن، والتفريغ، والتسخين، والضغط، والتبريد. |
المزايا | تقليل وقت المعالجة، وتحسين خصائص المواد، وكثافة قريبة من الكثافة النظرية. |
التطبيقات | المكونات الفضائية، وأدوات القطع، والركائز الإلكترونية. |
البيئة | يتم إجراؤها في فراغ أو غاز خامل لمنع الأكسدة. |
اعتبارات المواد | قوالب الجرافيت، توزيع موحد لحجم الجسيمات للمسحوق. |
اكتشف كيف يمكن للضغط الساخن أن يعزز إنتاج المواد الخاصة بك- اتصل بنا اليوم للحصول على إرشادات الخبراء!