التسخين بالحث هو طريقة فعالة وسريعة للغاية لتسخين المواد الموصلة للكهرباء عن طريق توليد الحرارة داخليًا من خلال الحث الكهرومغناطيسي.وتتطلب العملية مكونين أساسيين: مجال مغناطيسي متغير ومادة موصلة للكهرباء.وبالإضافة إلى هذه الأساسيات، يعتمد تصميم نظام التسخين بالحث وكفاءته على عدة عوامل، بما في ذلك خصائص المادة، ومصدر طاقة النظام، وتصميم الملف الحثي، ومتطلبات التطبيق المحددة.هذه الطريقة متعددة الاستخدامات، مما يسمح بالتسخين في بيئات مختلفة دون تلامس مباشر، مما يجعلها مثالية للتطبيقات التي يكون فيها التلوث مصدر قلق.
شرح النقاط الرئيسية:
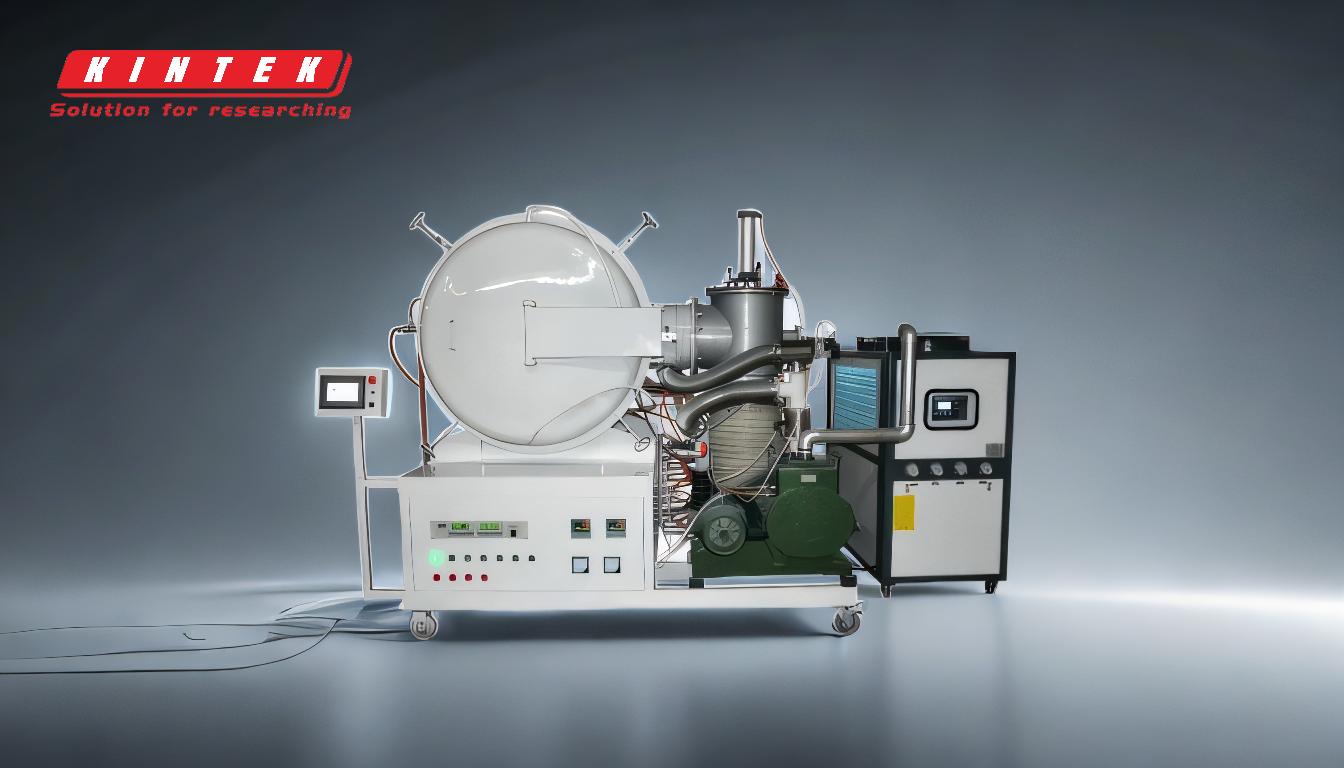
-
المتطلبات الأساسية للتدفئة التعريفي:
- :: تغيير المجال المغناطيسي:أحد المتطلبات الرئيسية هو وجود مجال مغناطيسي متغير، وعادةً ما يتم إنشاؤه بواسطة تيار متردد (AC) يمر عبر ملف محث.يستحث هذا المجال المغناطيسي تيارات دوامة في المادة الموصلة.
- مادة موصلة للكهرباء:يجب أن تكون المادة المراد تسخينها موصلة للكهرباء.يشيع استخدام معادن مثل الصلب والنحاس والألومنيوم.تولد التيارات الدوامة المستحثة حرارة بسبب المقاومة الكهربائية للمادة.
-
اعتبارات المواد:
- نوع المادة:يكون التسخين بالحث أكثر فعالية مع المعادن والمواد الموصلة الأخرى.تلعب مقاومة المادة دورًا مهمًا؛ فالمواد ذات المقاومة العالية تسخن بشكل أسرع بسبب المقاومة الأكبر للتيارات المستحثة.
- الحجم والسمك:تسخن المواد الأصغر حجماً والأقل سمكاً بسرعة أكبر من المواد الأكبر حجماً أو الأكثر سمكاً.ويرجع ذلك إلى أن التيارات المستحثة يمكن أن تخترق بفعالية أكبر، وتتركز الحرارة المتولدة في حجم أصغر.
-
تردد التيار المتردد:
- عمق التدفئة:يؤثر تردد التيار المتردد المستخدم في ملف الحث على عمق التسخين.تؤدي الترددات الأعلى إلى أعماق تسخين أقل عمقًا، وهو أمر مثالي لتطبيقات التسخين السطحي.الترددات المنخفضة مناسبة بشكل أفضل لاختراق أعمق في المواد الأكثر سمكًا.
-
تصميم ملف الحث:
- تكوين الملف:تصميم ملف الحث أمر بالغ الأهمية للتسخين الفعال.يجب تشكيل الملف ووضعه لضمان التوزيع الأمثل للمجال المغناطيسي حول المادة.غالبًا ما تكون تصميمات الملفات المخصصة مطلوبة لتطبيقات محددة.
- الكفاءة:تتأثر كفاءة نظام التسخين بالحث الحثي بتصميم المحرِّض.يقلل التصميم المناسب للملف من فقدان الطاقة ويضمن تسخينًا موحدًا.
-
سعة إمداد الطاقة:
- متطلبات الطاقة:يجب أن يكون مصدر الطاقة قادرًا على توصيل طاقة كافية لتحقيق الارتفاع المطلوب في درجة الحرارة.يعتمد ذلك على الحرارة النوعية للمادة والكتلة والتغير المطلوب في درجة الحرارة.
- اعتبارات فقدان الحرارة:يجب أن يراعي مصدر الطاقة أيضًا فقدان الحرارة بسبب التوصيل والحمل الحراري والإشعاع.يمكن أن يساعد عزل المادة أو بيئة التسخين في تقليل هذه الخسائر.
-
الاعتبارات البيئية:
- تعدد الاستخدامات:يمكن إجراء التسخين التعريفي في بيئات مختلفة، بما في ذلك السوائل أو الغازات أو حتى في الفراغ.هذا التنوع يجعله مناسبًا للتطبيقات التي يكون فيها التلوث أو التلامس المباشر مع مصدر الحرارة مصدر قلق.
- العزل:يمكن تغطية المادة بمادة عازلة أو غمرها في سائل دون التأثير على عملية التسخين، حيث لا يوجد تلامس مباشر مع مصدر الحرارة.
-
الكفاءة والمتطلبات الخاصة بالتطبيق:
- التباين في درجة الحرارة:تعتمد كفاءة التسخين بالحث على درجة تغير درجة الحرارة المطلوبة.قد تحتاج التطبيقات التي تتطلب نطاقًا واسعًا من التغيرات في درجات الحرارة إلى مزيد من الطاقة لتحقيق النتائج المرجوة.
- كفاءة النظام:تتأثر الكفاءة الكلية للنظام بخصائص المادة وتصميم المحرِّض وسعة إمداد الطاقة.ويضمن تحسين هذه العوامل تحقيق التسخين الفعال والموفر للطاقة.
في الختام، يعد التسخين بالحث الحثي طريقة متعددة الاستخدامات وفعالة لتسخين المواد الموصلة للكهرباء مع متطلبات واعتبارات محددة يجب معالجتها لتحقيق أفضل النتائج.من خلال فهم النظام وتصميمه بعناية حول خصائص المواد وإمدادات الطاقة والعوامل البيئية، يمكن استخدام التسخين بالحث بفعالية في مجموعة واسعة من التطبيقات الصناعية والتصنيعية.
جدول ملخص:
الجانب الرئيسي | التفاصيل |
---|---|
المتطلبات الأساسية | مجال مغناطيسي متغير، مادة موصلة للكهرباء |
اعتبارات المواد | نوع المادة ومقاومتها وحجمها وسماكتها |
تردد التيار المتردد | ترددات أعلى للتسخين السطحي؛ ترددات أقل لتسخين أعمق |
تصميم لفائف الحث | تصميمات مخصصة للتوزيع الأمثل للمجال المغناطيسي والكفاءة المثلى |
قدرة إمداد الطاقة | طاقة كافية لتحقيق الارتفاع المرغوب في درجة الحرارة، مع مراعاة فقدان الحرارة |
الاعتبارات البيئية | بيئات متعددة الاستخدامات (سوائل، غازات، تفريغ الهواء)، خيارات العزل |
عوامل الكفاءة | خصائص المواد وتصميم المحرِّض ومصدر الطاقة ونطاق درجة الحرارة |
اكتشف كيف يمكن للتسخين بالحث الحثي تحسين عملياتك- اتصل بخبرائنا اليوم !