الكربنة هي عملية معالجة حرارية تُدخل الكربون إلى سطح الفولاذ منخفض الكربون لتعزيز صلابته ومقاومته للتآكل. هناك خمس طرق أساسية للكربنة، ولكل منها خصائصها ومزاياها وتطبيقاتها الفريدة. تتضمن هذه الطرق كربنة العبوة، وكربنة الغاز، وكربنة السائل، وكربنة الفراغ، وكربنة البلازما. تختلف كل تقنية من حيث الوسط المستخدم لإدخال الكربون، والمعدات المطلوبة، والنتائج المحددة التي يتم تحقيقها. يعد فهم هذه الطرق أمرًا بالغ الأهمية لاختيار التقنية الأكثر ملاءمة بناءً على الخصائص المطلوبة للفولاذ ومتطلبات التطبيق المحددة.
وأوضح النقاط الرئيسية:
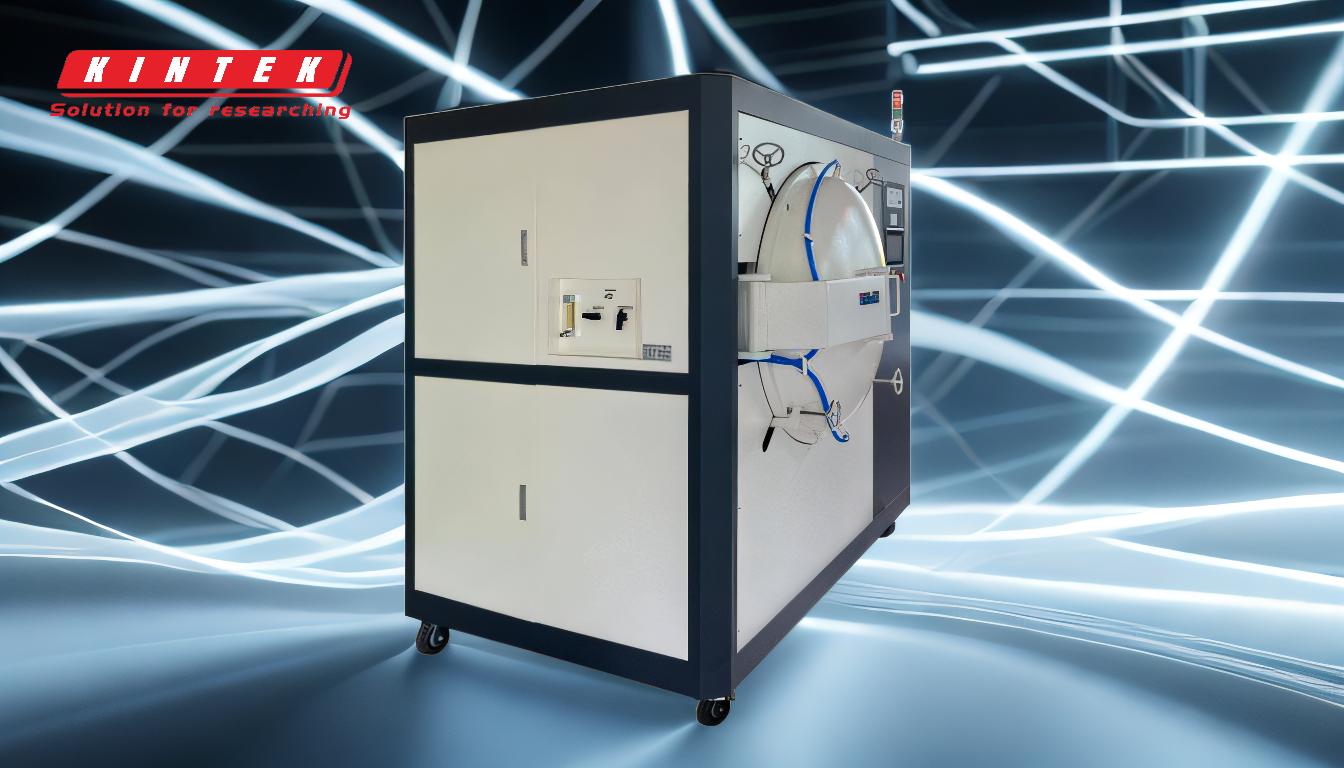
-
حزمة الكربنة
- عملية: في عملية الكربنة، يتم تعبئة الأجزاء الفولاذية في حاوية تحتوي على مادة غنية بالكربون، مثل الفحم أو فحم الكوك. يتم بعد ذلك تسخين الحاوية في الفرن إلى درجة حرارة تتراوح بين 900 درجة مئوية و950 درجة مئوية، مما يسمح للكربون بالانتشار في السطح الفولاذي.
- المزايا: هذه الطريقة فعالة من حيث التكلفة ومناسبة لدفعات كبيرة من الأجزاء. فهو يوفر عمقًا عميقًا للعلبة، وهو أمر مفيد للمكونات التي تتطلب مقاومة كبيرة للتآكل.
- العيوب: تستغرق العملية وقتًا طويلاً، ومن الصعب التحكم بدقة في إمكانات الكربون. بالإضافة إلى ذلك، قد تتطلب الأجزاء تنظيفًا إضافيًا بعد العملية بسبب مواد التغليف الغنية بالكربون.
-
كربنة الغاز
- عملية: تتضمن كربنة الغاز تسخين الأجزاء الفولاذية في فرن به جو غازي غني بالكربون، وعادةً ما يكون خليطًا من الميثان أو البروبان أو الغاز الطبيعي. يتم الحفاظ على درجة الحرارة بين 850 درجة مئوية و950 درجة مئوية، مما يسمح للكربون بالانتشار في سطح الفولاذ.
- المزايا: توفر هذه الطريقة تحكمًا أفضل في إمكانات الكربون وعمق العلبة مقارنةً بالكربنة الموجودة في العبوة. كما أنها أسرع وأكثر كفاءة، مما يجعلها مناسبة للإنتاج بكميات كبيرة.
- العيوب: المعدات اللازمة لكربنة الغاز أكثر تعقيدًا وتكلفة. بالإضافة إلى ذلك، تتطلب العملية مراقبة دقيقة لتكوين الغاز لضمان الحصول على نتائج متسقة.
-
الكربنة السائلة
- عملية: الكربنة السائلة، والمعروفة أيضًا باسم الكربنة بحمام الملح، تتضمن غمر الأجزاء الفولاذية في حمام ملح منصهر يحتوي على مركبات غنية بالكربون، مثل سيانيد الصوديوم أو سيانيد البوتاسيوم. يتم الحفاظ على درجة الحرارة عادة بين 850 درجة مئوية و950 درجة مئوية.
- المزايا: توفر هذه الطريقة تسخينًا سريعًا وموحدًا، مما يؤدي إلى عمق متسق للعلبة وتركيز الكربون. كما أنها مناسبة للأجزاء الصغيرة والمعقدة.
- العيوب: استخدام الأملاح القائمة على السيانيد يشكل مخاوف بيئية وسلامية. بالإضافة إلى ذلك، تتطلب الأجزاء تنظيفًا شاملاً بعد العملية لإزالة أي أملاح متبقية.
-
الكربنة الفراغية
- عملية: يتم تنفيذ الكربنة الفراغية في فرن فراغ، حيث يتم تسخين الأجزاء الفولاذية إلى درجات حرارة تتراوح بين 900 درجة مئوية و1050 درجة مئوية في بيئة منخفضة الضغط. يتم إدخال غاز غني بالكربون، مثل الميثان أو البروبان، إلى الفرن لتسهيل انتشار الكربون.
- المزايا: توفر هذه الطريقة تحكمًا ممتازًا في إمكانات الكربون وعمق العلبة، مما يؤدي إلى نتائج متسقة وعالية الجودة. كما أنه يزيل خطر الأكسدة ونزع الكربنة، حيث تتم العملية في الفراغ.
- العيوب: المعدات اللازمة لعملية الكربنة الفراغية باهظة الثمن، والعملية أبطأ مقارنة بالطرق الأخرى. يتم استخدامه عادةً للمكونات عالية القيمة حيث تكون الدقة والجودة أمرًا بالغ الأهمية.
-
كربنة البلازما
- عملية: تتضمن كربنة البلازما، والمعروفة أيضًا بالكربنة الأيونية، وضع الأجزاء الفولاذية في حجرة مفرغة وإدخال غاز غني بالكربون، مثل الميثان. يتم إنشاء البلازما عن طريق تطبيق مجال كهربائي عالي الجهد، مما يؤدي إلى تأين الغاز وتسريع أيونات الكربون نحو سطح الفولاذ.
- المزايا: توفر هذه الطريقة تحكمًا دقيقًا في إمكانات الكربون وعمق العلبة، مما يؤدي إلى كربنة موحدة وعالية الجودة. كما أنها أسرع وأكثر كفاءة في استخدام الطاقة مقارنة بالطرق التقليدية.
- العيوب: المعدات اللازمة لكربنة البلازما معقدة ومكلفة. بالإضافة إلى ذلك، تقتصر العملية على أجزاء صغيرة ومتوسطة الحجم بسبب قيود حجم غرفة الفراغ.
في الختام، يعتمد اختيار طريقة الكربنة على عوامل مختلفة، بما في ذلك الخصائص المطلوبة للصلب، وحجم الأجزاء وتعقيدها، وحجم الإنتاج، واعتبارات التكلفة. تتمتع كل طريقة بمزاياها وقيودها الفريدة، مما يجعل من الضروري اختيار التقنية الأكثر ملاءمة بناءً على المتطلبات المحددة للتطبيق.
جدول ملخص:
طريقة | نظرة عامة على العملية | المزايا | العيوب |
---|---|---|---|
حزمة الكربنة | الأجزاء الفولاذية معبأة بمواد غنية بالكربون، ويتم تسخينها إلى 900-950 درجة مئوية. | فعالة من حيث التكلفة، وعمق الحالة العميق. | التحكم في الكربون صعب ومستهلك للوقت. |
كربنة الغاز | يتم تسخين الفولاذ في جو غازي غني بالكربون (850-950 درجة مئوية). | تحكم أفضل في الكربون، وأسرع للحجم الكبير. | معدات باهظة الثمن، وتتطلب مراقبة الغاز. |
الكربنة السائلة | الصلب المغمور في حمام الملح المنصهر مع مركبات الكربون (850-950 درجة مئوية). | تسخين سريع وموحد، مثالي للأجزاء الصغيرة. | المخاوف البيئية/السلامة، بعد التنظيف. |
الكربنة الفراغية | يتم تسخين الفولاذ في فرن فراغي بغاز غني بالكربون (900-1050 درجة مئوية). | تحكم دقيق، لا يوجد خطر أكسدة. | عملية مكلفة وأبطأ. |
كربنة البلازما | الصلب في غرفة مفرغة مع غاز غني بالكربون المتأين (البلازما). | كفاءة في استخدام الطاقة، نتائج موحدة. | المعدات المعقدة، تقتصر على الأجزاء الصغيرة والمتوسطة. |
هل تحتاج إلى مساعدة في اختيار طريقة الكربنة المناسبة لتطبيقك؟ اتصل بخبرائنا اليوم !