المعالجة الحرارية للصلب هي عملية حاسمة تستخدم لتغيير خصائصه الفيزيائية والميكانيكية، مثل الصلابة والمتانة والليونة والقوة. تتضمن العملية ثلاث مراحل أساسية: التسخين والنقع والتبريد. تلعب كل مرحلة دورًا حيويًا في تحقيق خصائص المادة المطلوبة. تقوم مرحلة التسخين برفع الفولاذ إلى درجة حرارة معينة، وتحافظ مرحلة النقع على درجة الحرارة هذه لضمان تغيرات هيكلية موحدة، وتقوم مرحلة التبريد بترسيخ هذه التغييرات. يمكن تصميم هذه المراحل لتحقيق نتائج محددة، مثل التلدين للحصول على النعومة أو التبريد للحصول على الصلابة. يعد فهم هذه المراحل أمرًا ضروريًا لتحسين أداء الفولاذ في التطبيقات المختلفة.
وأوضح النقاط الرئيسية:
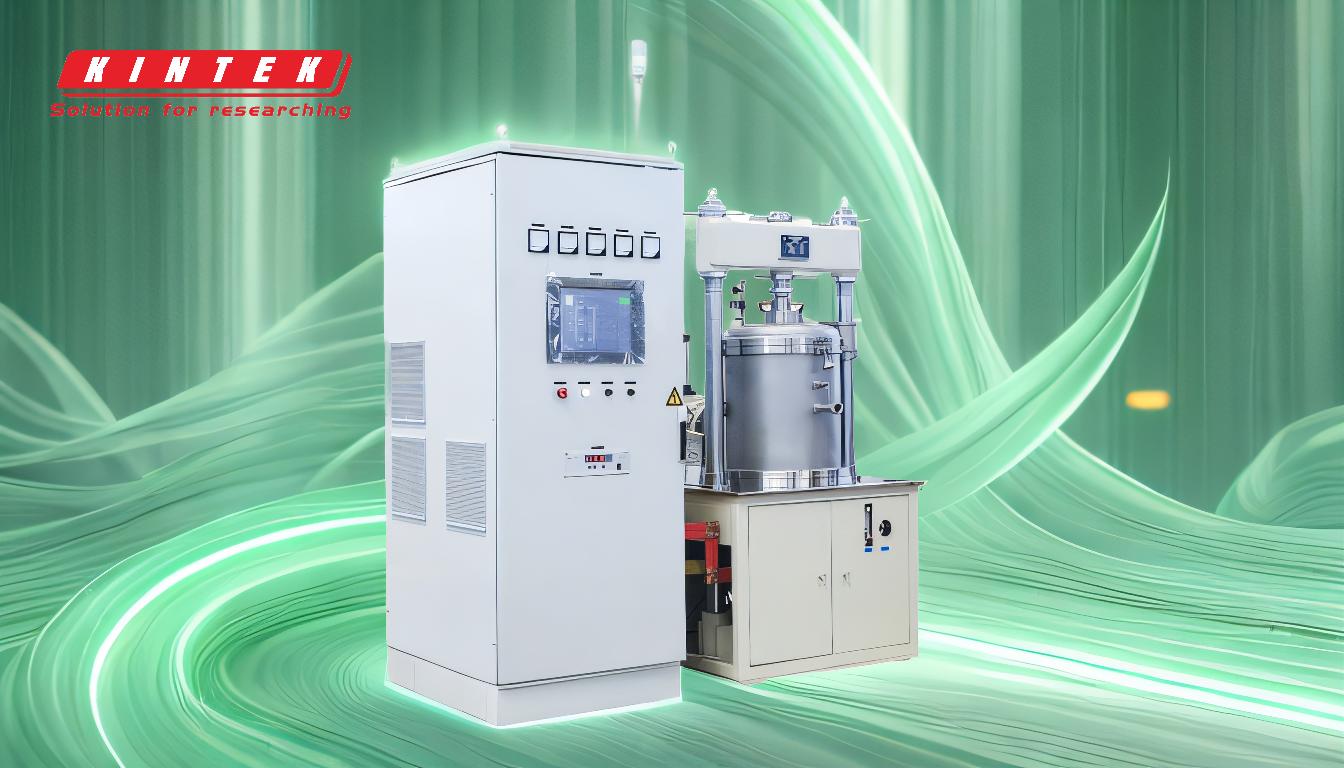
-
مرحلة التدفئة:
- تتضمن المرحلة الأولى تسخين الفولاذ إلى درجة حرارة محددة مسبقًا، والتي يمكن أن تتراوح من بضع مئات من الدرجات إلى 2400 درجة فهرنهايت، اعتمادًا على النتيجة المرجوة.
- غاية: يضمن التسخين وصول الفولاذ إلى درجة حرارة يبدأ فيها هيكله الداخلي بالتغير، مما يجعله أكثر مرونة أو يجهزه لمزيد من التحولات.
- اعتبارات: يجب التحكم في معدل التسخين بعناية لتجنب الإجهاد الحراري الذي قد يؤدي إلى الاعوجاج أو التشقق. يعد التسخين الموحد أمرًا بالغ الأهمية لضمان نتائج متسقة.
-
مرحلة النقع:
- بمجرد وصول الفولاذ إلى درجة الحرارة المستهدفة، يتم الاحتفاظ به عند درجة الحرارة هذه لمدة محددة، تعرف باسم وقت النقع.
- غاية: يسمح النقع للحرارة بالتغلغل بشكل موحد في جميع أنحاء المادة، مما يضمن خضوع قطعة العمل بأكملها للتغييرات الهيكلية المطلوبة.
- اعتبارات: يمكن أن يختلف وقت النقع بشكل كبير، من بضع ثوانٍ إلى عدة ساعات، اعتمادًا على تركيبة الفولاذ والاستخدام المقصود. يضمن النقع المناسب التجانس في خصائص المادة.
-
مرحلة التبريد:
- بعد النقع، يتم تبريد الفولاذ وفقًا لطريقة محددة، والتي يمكن أن تتضمن التبريد السريع، أو التبريد البطيء في الفرن، أو التبريد المتحكم فيه في الهواء.
- غاية: يحدد معدل التبريد الخواص النهائية للصلب. عادةً ما يؤدي التبريد السريع (التبريد) إلى زيادة الصلابة، بينما يؤدي التبريد البطيء (التليين) إلى تعزيز الليونة وتقليل الضغوط الداخلية.
- اعتبارات: يجب اختيار طريقة التبريد بعناية لتحقيق التوازن المطلوب بين الصلابة والمتانة وغيرها من الخصائص. التبريد غير السليم يمكن أن يؤدي إلى هشاشة أو الضغوط المتبقية.
-
أنواع عمليات المعالجة الحرارية:
- الصلب: يتضمن تسخين الفولاذ إلى درجة حرارة معينة ثم تبريده ببطء لتليين المادة وتحسين الليونة وتخفيف الضغوط الداخلية.
- التبريد: يبرد الفولاذ بسرعة لزيادة صلابته وقوته، وغالبًا ما يتبعه تقسية لتقليل الهشاشة.
- هدأ: إعادة تسخين الفولاذ المروي إلى درجة حرارة أقل لتحسين المتانة وتقليل الهشاشة مع الحفاظ على الصلابة.
- تصلب القضية: يضيف طبقة سطحية صلبة إلى الفولاذ مع الحفاظ على قلب أكثر ليونة وصلابة، مما يعزز مقاومة التآكل.
- الكربنة: يدخل الكربون في الطبقة السطحية من الفولاذ لزيادة صلابة السطح ومقاومة التآكل.
- تصلب هطول الأمطار: يقوي الفولاذ من خلال تكوين جزيئات دقيقة داخل المادة، مما يحسن القوة والصلابة دون تقليل الليونة بشكل كبير.
-
التطبيقات والاعتبارات:
- صناعة الطيران: تعتبر المعالجة الحرارية أمرًا بالغ الأهمية للمكونات التي تتطلب نسب قوة إلى وزن عالية ومقاومة للظروف القاسية.
- صناعة السيارات: يستخدم لتعزيز متانة وأداء أجزاء المحرك والتروس ومكونات نظام التعليق.
- تصنيع الأدوات: تضمن المعالجة الحرارية أن تتمتع الأدوات بالصلابة اللازمة ومقاومة التآكل لعمليات القطع والتشكيل والتشكيل.
- التخصيص: يمكن تصميم عملية المعالجة الحرارية لتلبية متطلبات محددة، مثل التصلب الموضعي أو تخفيف الضغط في مناطق معينة من المكون.
من خلال فهم مراحل المعالجة الحرارية والتحكم فيها بعناية، يمكن للمصنعين تحسين خصائص الفولاذ لمجموعة واسعة من التطبيقات، مما يضمن المتانة والأداء وطول العمر.
جدول ملخص:
منصة | غاية | الاعتبارات الرئيسية |
---|---|---|
التدفئة | رفع الفولاذ إلى درجة حرارة محددة لإجراء التغييرات الهيكلية. | التحكم في معدل التسخين لتجنب التشويه؛ ضمان تسخين موحد للحصول على نتائج متسقة. |
تمرغ | الحفاظ على درجة الحرارة لاختراق الحرارة موحدة. | يختلف وقت النقع بناءً على تركيبة الفولاذ ومتطلبات التطبيق. |
تبريد | ترسيخ التغييرات الهيكلية من خلال طرق التبريد الخاضعة للرقابة. | يحدد معدل التبريد الخصائص النهائية (مثل الصلابة والمتانة). |
هل تحتاج إلى إرشادات الخبراء بشأن المعالجة الحرارية لتطبيقات الفولاذ لديك؟ اتصل بنا اليوم لتحسين العملية الخاصة بك!