الترسيب بالتبخير الحراري هو عملية يتم فيها تسخين مادة صلبة في غرفة تفريغ عالية لإنتاج ضغط بخار يؤدي إلى تكوين طبقة رقيقة على الركيزة. وتختلف درجة الحرارة المطلوبة لهذه العملية اعتمادًا على المادة التي يتم تبخيرها، حيث أن كل مادة لها منحنى ضغط بخار فريد من نوعه. وعمومًا، يجب أن تكون درجة الحرارة مرتفعة بما يكفي لتوليد ضغط بخار كافٍ للترسيب ولكن يجب أيضًا مراعاة الاستقرار الحراري وخصائص كل من المادة المصدر والركيزة. درجة حرارة العملية هي معلمة حاسمة تؤثر على معدل الترسيب وجودة الفيلم والخصائص النهائية للفيلم المترسب.
شرح النقاط الرئيسية:
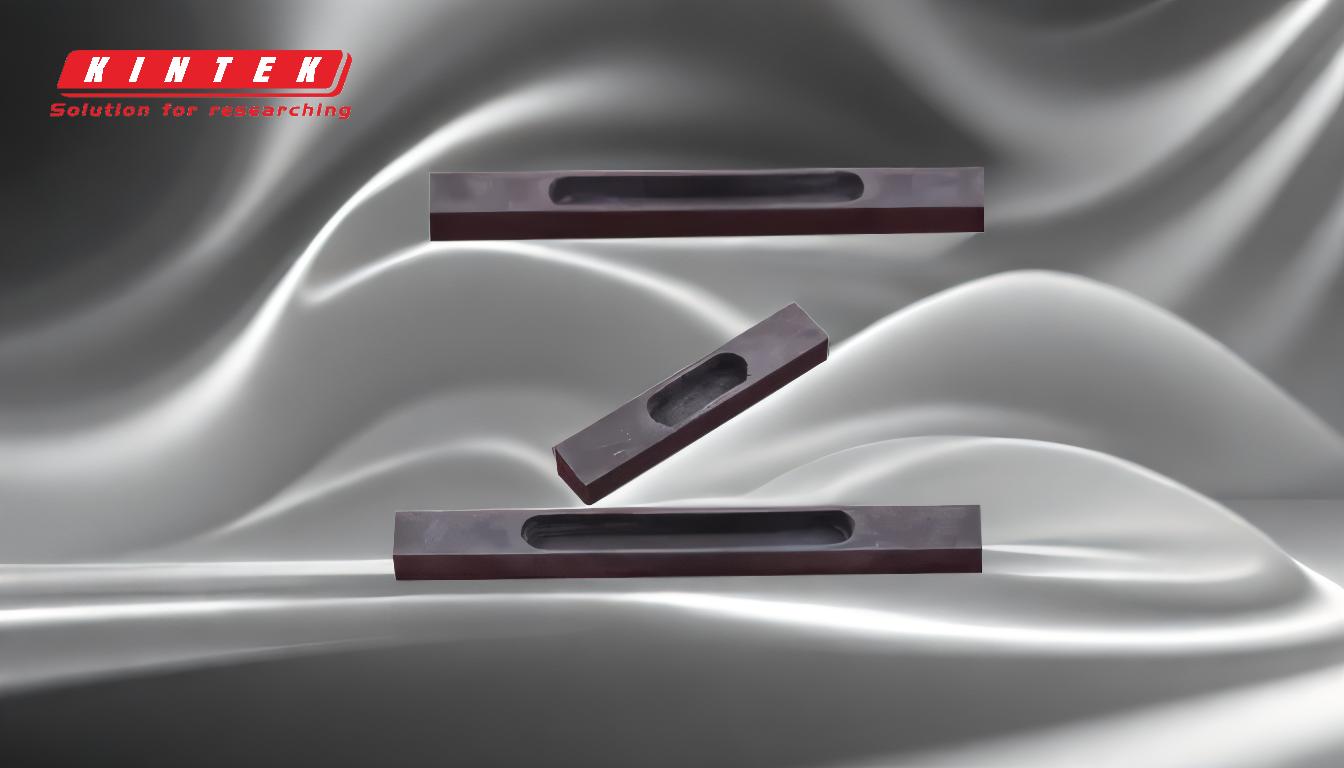
-
العلاقة بين درجة الحرارة وضغط البخار:
- ترتبط درجة حرارة الترسيب بالتبخير الحراري ارتباطًا مباشرًا بضغط بخار المادة التي يتم تبخيرها. ويؤدي ارتفاع درجات الحرارة إلى زيادة ضغط البخار، مما يؤدي إلى زيادة كفاءة التبخير والترسيب.
- لكل مادة نطاق درجة حرارة محددة تنتقل عنده من الطور الصلب إلى الطور البخاري، وهو ما يعرف بدرجة حرارة التبخر. ويتم تحديد درجة الحرارة هذه من خلال منحنى ضغط بخار المادة.
-
درجات حرارة التبخر الخاصة بالمواد:
- تتطلب المواد المختلفة درجات حرارة تبخر مختلفة. على سبيل المثال، تتبخر المعادن مثل الألومنيوم عند حوالي 1200 درجة مئوية، في حين أن المواد العضوية قد تتبخر عند درجات حرارة أقل بكثير، وغالبًا ما تكون أقل من 300 درجة مئوية.
- يعتمد اختيار المواد للترسيب بالتبخير الحراري على خصائص تفاعلها واستقرارها الحراري. تتطلب المواد ذات درجات الانصهار العالية درجات حرارة تبخير أعلى.
-
أثر درجة الحرارة على معدل الترسيب وجودة الفيلم:
- تؤدي درجات الحرارة المرتفعة عمومًا إلى معدلات ترسيب أعلى بسبب زيادة ضغط البخار. ومع ذلك، يمكن أن تؤدي درجات الحرارة المرتفعة للغاية إلى مشاكل مثل تحلل المواد أو التفاعلات غير المرغوب فيها.
- يجب التحكم في درجة الحرارة بعناية لضمان سمك موحد للفيلم وقوة الالتصاق والخصائص البصرية أو الكهربائية المطلوبة.
-
بيئة التفريغ والتحكم في درجة الحرارة:
- يحدث الترسيب بالتبخير الحراري في غرفة تفريغ عالية لتقليل الشوائب وضمان مسار حر متوسط طويل لجزيئات المادة المتبخرة.
- تسمح بيئة التفريغ بفعالية ضغوط البخار المنخفضة نسبيًا، مما يعني أنه حتى درجات الحرارة المعتدلة يمكن أن تحقق تبخرًا كافيًا.
-
اعتبارات الركيزة:
- يجب مراعاة الاستقرار الحراري للركيزة وخصائص السطح عند اختيار درجة حرارة التبخير. يمكن أن تؤدي درجات الحرارة العالية إلى تلف الركائز الحساسة أو تغيير خصائصها.
- ويلعب دوران الركيزة وخشونة السطح أيضًا دورًا في ضمان ترسيب موحد وجودة الفيلم.
-
نطاقات درجة الحرارة العملية:
- بالنسبة لمعظم المعادن، تتراوح درجات حرارة التبخير بين 1000 درجة مئوية إلى 2000 درجة مئوية، اعتمادًا على المادة.
- عادةً ما تتطلب المواد العضوية والبوليمرات عادةً درجات حرارة أقل بكثير، غالبًا ما تكون أقل من 500 درجة مئوية لتجنب التحلل.
-
آليات التحكم في درجة الحرارة:
- يتم تسخين زورق التبخير أو الفتيل باستخدام تيار كهربائي، ويتم تنظيم درجة الحرارة عن طريق ضبط مصدر الطاقة.
- قد تتضمن الأنظمة المتقدمة آليات تغذية مرتدة للحفاظ على التحكم الدقيق في درجة الحرارة، مما يضمن معدلات ترسيب متسقة وخصائص الفيلم.
باختصار، تعتبر درجة حرارة الترسيب بالتبخير الحراري معلمة حرجة تختلف باختلاف المادة التي يتم تبخيرها وخصائص الفيلم المطلوبة. يجب التحكم فيها بعناية لتحقيق التوازن بين معدل الترسيب وجودة الفيلم وسلامة الركيزة. يعد فهم العلاقة بين درجة الحرارة وضغط البخار وخصائص المواد أمرًا ضروريًا لتحسين عملية التبخير الحراري.
جدول ملخص:
العامل الرئيسي | الوصف |
---|---|
درجة الحرارة وضغط البخار | يزيد ارتفاع درجات الحرارة من ضغط البخار، مما يحسن من كفاءة التبخير. |
درجات الحرارة الخاصة بالمواد | تحتاج المعادن (مثل الألومنيوم) إلى 1200 درجة مئوية تقريبًا؛ بينما تحتاج المواد العضوية إلى أقل من 300 درجة مئوية. |
معدل الترسيب وجودة الفيلم | تضمن درجة الحرارة المتحكّم بها سمكًا موحّدًا وخصائص مرغوبة. |
بيئة الفراغ | يقلل التفريغ العالي من الشوائب ويتيح التبخير الفعال. |
اعتبارات الركيزة | يجب أن يتماشى الثبات الحراري وخصائص السطح مع درجة حرارة التبخر. |
نطاقات درجة الحرارة العملية | المعادن: 1000 درجة مئوية - 2000 درجة مئوية؛ المواد العضوية: <500°C. |
آليات التحكم في درجة الحرارة | يعمل التيار الكهربائي على تسخين قارب التبخير، مع وجود تغذية راجعة للدقة. |
هل تحتاج إلى مساعدة في تحسين عملية الترسيب بالتبخير الحراري؟ تواصل مع خبرائنا اليوم !