تلبيد البلازما الشرارة الملبدة (SPS) هي تقنية تلبيد متقدمة تستخدم التيار المباشر النبضي (DC) لتكثيف مواد المسحوق بسرعة.تتضمن العملية تطبيق تيار نابض على جزيئات المسحوق، مما يولد درجات حرارة عالية موضعية وبلازما وتسخين جول.ويسهّل هذا التنشيط لأسطح الجسيمات والتسخين الداخلي التكثيف السريع في درجات حرارة منخفضة مقارنة بطرق التلبيد التقليدية.وتُعرف تقنية SPS بقدرتها على إنتاج مواد عالية الكثافة وعالية القوة مع بنى مجهرية دقيقة في وقت قصير.على الرغم من اسمها، تشير الأبحاث إلى أن توليد البلازما ليس الآلية الأساسية، مما يؤدي إلى أسماء بديلة مثل تقنية التلبيد بمساعدة المجال (FAST) أو التلبيد بالتيار المباشر (DCS).تُستخدم SPS على نطاق واسع في أبحاث المواد المتقدمة، بما في ذلك السيراميك النانوي والمواد المغناطيسية والمواد المركبة.
شرح النقاط الرئيسية:
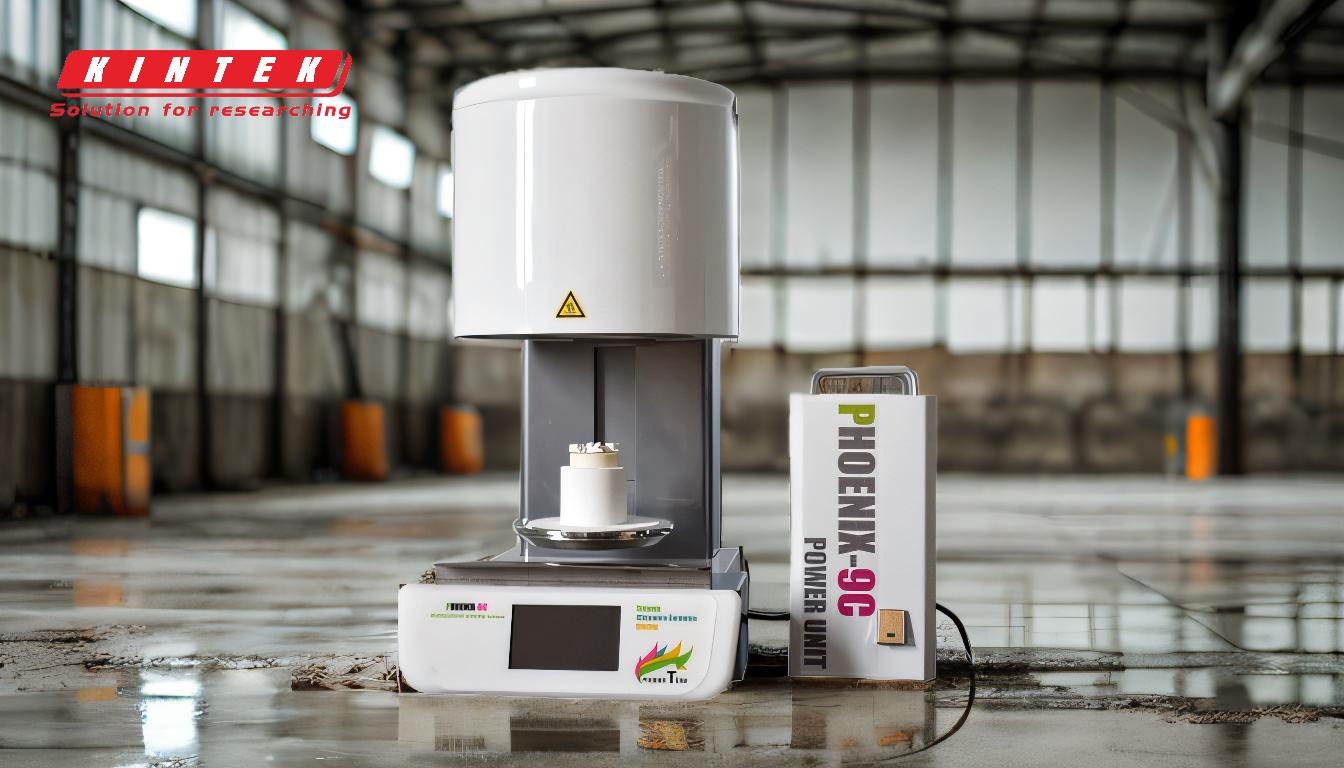
-
مبدأ التلبيد بالبلازما الشرارة (SPS):
- يستخدم SPS تيار تيار مستمر نابض لتوليد بلازما التفريغ وحرارة جول وانتشار المجال الكهربائي.
- ينشط التيار النبضي أسطح الجسيمات ويخلق تسخينًا داخليًا موحدًا، مما يتيح التكثيف السريع.
- تقلل هذه العملية من فجوات الجسيمات وتعزز الانتشار السطحي والحدودي، مما يؤدي إلى ترابط قوي بين الجسيمات.
-
آلية التيار النبضي في SPS:
- يتم تطبيق التيار المستمر النبضي من خلال قالب موصل (عادةً ما يكون من الجرافيت)، وإذا أمكن، من خلال المادة نفسها.
- ويعمل القالب كمصدر حرارة خارجي وداخلي على حد سواء، مما يسمح بمعدلات تسخين وتبريد سريعة.
- ويتسبب التيار العالي اللحظي في ارتفاع درجات الحرارة والبلازما الموضعية العالية، مما يذيب واجهات الجسيمات ويربطها معًا.
-
مزايا SPS:
- انخفاض درجات حرارة التلبيد: يحقق SPS التكثيف عند درجات حرارة أقل بعدة مئات من الدرجات من الطرق التقليدية.
- أوقات معالجة أقصر: العملية أسرع بكثير بسبب التسخين والتبريد السريع.
- مواد عالية الكثافة وعالية القوة: تنتج SPS مواد ذات بنية مجهرية دقيقة وأقل مسامية.
- تعدد الاستخدامات: مناسبة لمجموعة واسعة من المواد، بما في ذلك السيراميك والمعادن والمواد المركبة.
-
المفاهيم الخاطئة حول البلازما في SPS:
- على الرغم من التسمية، تُظهر الأبحاث أن توليد البلازما ليس آلية أساسية في SPS.
- وتعتبر الأسماء البديلة مثل تقنية التلبيد بمساعدة المجال (FAST) أو التلبيد بالتيار المباشر (DCS) أكثر دقة.
- الآليات الأساسية هي تسخين جول والانتشار بمساعدة المجال الكهربائي.
-
تطبيقات SPS:
- المواد المغناطيسية: تُستخدم SPS لإنتاج مواد مغناطيسية عالية الأداء ذات بنى مجهرية محكومة.
- السيراميك النانوي: تُعد هذه التقنية مثالية لتلبيد السيراميك النانوي، مع الحفاظ على خصائصها النانوية.
- المواد الوظيفية المتدرجة: تتيح SPS إنشاء مواد ذات خصائص متدرجة للتطبيقات المتخصصة.
- المركبات بين الفلزات: يستخدم لتلبيد المركبات بين الفلزية ذات الخواص الميكانيكية المحسنة.
-
التطور التاريخي لتكنولوجيا SPS:
- اقترحت تقنية SPS لأول مرة في ثلاثينيات القرن العشرين، لكنها اكتسبت تطبيقًا عمليًا في الستينيات في الولايات المتحدة واليابان.
- وقد تم تطوير أول جهاز صناعي يعمل بتقنية SPS في اليابان في عام 1988، مما أدى إلى اعتمادها على نطاق واسع في أبحاث المواد المتقدمة.
- يُعرف جهاز SPS بسرعته وتشغيله في درجات حرارة منخفضة وكفاءته في استخدام الطاقة.
-
الفوائد البيئية والطاقة:
- تعتبر تقنية SPS تقنية موفرة للطاقة وصديقة للبيئة.
- تقلل العملية من استهلاك الطاقة ووقت المعالجة مقارنة بطرق التلبيد التقليدية.
- وتساهم قدرتها على العمل في درجات حرارة منخفضة في تقليل انبعاثات الكربون.
من خلال الجمع بين التيار النبضي والضغط الأحادي المحور، تقدم تقنية SPS نهجًا فريدًا للتلبيد يعالج العديد من القيود التي تواجه الطرق التقليدية.إن قدرتها على إنتاج مواد عالية الجودة ذات بنى مجهرية دقيقة في وقت قصير تجعلها أداة قيمة في أبحاث المواد المتقدمة والتطبيقات الصناعية.
جدول ملخص:
الجانب الرئيسي | التفاصيل |
---|---|
المبدأ | يستخدم تيار تيار مستمر نابض للبلازما وحرارة جول وانتشار المجال الكهربائي. |
الآلية | تسخين وتبريد سريع عبر قالب موصل؛ درجات حرارة عالية موضعية. |
المزايا | درجات حرارة تلبيد أقل، وأوقات معالجة أقصر، وبنى مجهرية دقيقة. |
التطبيقات | المواد المغناطيسية، والسيراميك النانوي، والمواد الوظيفية المتدرجة، والمركبات. |
الفوائد البيئية | موفرة للطاقة، وتقلل من انبعاثات الكربون ووقت المعالجة. |
أطلق العنان لإمكانات تلبيد البلازما الشرارة لأبحاث المواد الخاصة بك- اتصل بخبرائنا اليوم !