المبادئ الأساسية لعملية الطلاء بالطباعة بالانبعاثات الكهروضوئية
التبخير
في بيئة مفرغة من الهواء، تخضع المادة الصلبة، المعروفة باسم الهدف، لعملية تحول إلى حالتها الغازية من خلال طرق مختلفة، تتضمن في المقام الأول التسخين. تُعرف هذه العملية باسم التبخر، وهي أساسية في عملية الطلاء بالترسيب الفيزيائي للبخار (PVD). وتُستخدم عدة تقنيات لتحقيق هذا التحول:
-
التبخير الحراري: تتضمن هذه الطريقة تسخين المادة المستهدفة إلى درجة حرارة التبخير باستخدام المقاومة الكهربائية أو عناصر تسخين أخرى. وبمجرد أن تصل المادة إلى نقطة تبخيرها، تتحول إلى غاز، ثم ينتشر ويتكثف على الركيزة لتشكيل طبقة رقيقة.
-
التبخير بالحزمة الإلكترونية: هنا، يتم توجيه شعاع إلكترون عالي الطاقة نحو المادة المستهدفة، مما يؤدي إلى تبخرها. وتعد هذه التقنية مفيدة بشكل خاص للمواد ذات درجات انصهار عالية، حيث يسمح تأثير التسخين الموضعي بالتحكم الدقيق في عملية التبخر.
-
التبخير بالليزر: باستخدام نبضات ليزر عالية الطاقة، تعمل هذه الطريقة على تبخير المادة المستهدفة. التبخير بالليزر مفيد لتحضير مواد الأغشية الرقيقة المعقدة، حيث يوفر دقة عالية ويمكن استخدامه لتبخير المواد التي يصعب التعامل معها بالطرق التقليدية.
لكل طريقة من هذه الطرق مزاياها الفريدة ويتم اختيارها بناءً على المتطلبات المحددة لعملية الطلاء، مثل نوع المادة المستخدمة والخصائص المرغوبة للفيلم الناتج.
النقل
تخضع المادة الغازية، بمجرد تحولها إلى حالة بخار، للانتشار داخل غرفة التفريغ. ويعد هذا الانتشار مرحلة حرجة في عملية التفريغ بالانبعاثات الكهروضوئية الطيفية، حيث يؤثر بشكل مباشر على انتظام وجودة ترسيب الفيلم اللاحق. هناك عدة عوامل رئيسية تؤثر بشكل كبير على مرحلة النقل هذه:
-
ضغط الغاز: يلعب الضغط داخل غرفة التفريغ دورًا محوريًا. وعادةً ما تعمل الضغوط المنخفضة على تعزيز كفاءة الانتشار، مما يضمن انتشار المادة الغازية بشكل أكثر اتساقًا عبر الركيزة. وعلى العكس من ذلك، يمكن أن تؤدي الضغوط المرتفعة إلى حدوث تصادمات بين جزيئات الغاز، مما قد يقلل من معدل الانتشار الكلي ويؤثر على انتظام الفيلم.
-
درجة الحرارة: تعد درجة الحرارة داخل بيئة التفريغ متغيرًا حاسمًا آخر. يمكن أن تؤدي درجات الحرارة المرتفعة إلى تسريع عملية الانتشار، ولكن يجب التحكم فيها بعناية لمنع حدوث تلف حراري للركيزة أو تكوين رواسب غير منتظمة. إن موازنة درجة الحرارة مع معلمات العملية الأخرى أمر ضروري لتحقيق الانتشار الأمثل.
-
موضع الركيزة: الترتيب المكاني للركيزة بالنسبة لمصدر المادة الغازية مهم أيضًا. تضمن المحاذاة المناسبة وصول المادة الغازية إلى جميع مناطق الركيزة بالتساوي، مما يمنع الترسيب الزائد أو الترسيب الناقص الموضعي. يمكن أن تساعد تقنيات مثل تدوير الركيزة أو إمالتها في تحقيق تغطية أكثر اتساقًا.
باختصار، إن نقل المواد الغازية في التفريغ هو عملية دقيقة تتطلب تحكمًا دقيقًا في ضغط الغاز ودرجة الحرارة ووضع الركيزة لضمان الترسيب الناجح لفيلم عالي الجودة.
الترسيب
أثناء مرحلة الترسيب، تبدأ المادة الغازية، التي تم نقلها إلى الركيزة، في التبريد والتكثيف. وتعتبر عملية التبريد هذه حاسمة لأنها تحول الغاز إلى طبقة رقيقة صلبة تلتصق بسطح الركيزة. وعملية الترسيب ليست مجرد تغيير فيزيائي بل هي عملية تحويلية أيضًا، حيث تغير خصائص الركيزة بشكل كبير بناءً على التطبيق المحدد.
ويلعب نوع الغاز المستخدم أثناء عملية الترسيب دورًا محوريًا في تحديد البنية النهائية للفيلم وخصائصه. على سبيل المثال، غالبًا ما يتم استخدام الغازات الخاملة مثل الأرجون والهيليوم للحفاظ على نقاء الفيلم، مما يضمن عدم حدوث تفاعلات كيميائية غير مرغوب فيها. من ناحية أخرى، يتم إدخال غازات تفاعلية مثل الأكسجين والنيتروجين والفلور لإنشاء مركبات محددة مثل الأكاسيد والنتريد والفلوريدات، مما يعزز وظيفة الفيلم لتطبيقات معينة.
وعلاوة على ذلك، فإن ضغط الغاز في غرفة الترسيب هو معلمة حاسمة تؤثر على كل من معدل الترسيب وجودة الفيلم. وعادةً ما يؤدي انخفاض ضغط الغاز عادةً إلى أفلام أكثر كثافة وتجانسًا، وهو أمر مرغوب فيه للعديد من التطبيقات. وعلى العكس من ذلك، يمكن أن تؤدي ضغوط الغاز الأعلى إلى أفلام أكثر خشونة، والتي قد تكون مفيدة في سياقات معينة، مثل عندما تكون هناك حاجة إلى زيادة مساحة السطح لتحسين الالتصاق أو التفاعل.
وباختصار، فإن عملية الترسيب هي تفاعل متطور بين التبريد ونوع الغاز والضغط، حيث يتم التحكم في كل عامل بدقة لتحقيق خصائص الفيلم المطلوبة. ويضمن هذا التنسيق الدقيق أن يفي الفيلم الرقيق الناتج بالمعايير الصارمة التي تتطلبها مختلف الصناعات، من الإلكترونيات إلى البصريات وما بعدها.
الأنواع الرئيسية لعملية PVD
الترسيب بالتبخير
الترسيب بالتبخير هو تقنية متطورة تُستخدم لإنتاج الأغشية الرقيقة عن طريق تسخين المواد المستهدفة إلى درجة تبخيرها. هذه العملية فعالة بشكل خاص للمعادن وبعض السبائك، حيث يتم تحويلها من الحالة الصلبة إلى الحالة الغازية من خلال الطاقة الحرارية. وبعد ذلك تتكثف الذرات المتبخرة على الركيزة لتشكل طبقة رقيقة موحدة ومطابقة. ويتم إجراء هذه الطريقة عادةً في بيئة عالية التفريغ لتقليل التصادمات والتلوث، مما يضمن نقاء وسلامة الطبقة المودعة.
وتتمثل إحدى المزايا الرئيسية للترسيب بالتبخير في قدرته على إنشاء أغشية عالية الجودة ذات تجانس وتوافق ممتازين. هذه التقنية متعددة الاستخدامات وقادرة على ترسيب مجموعة واسعة من المواد، بما في ذلك المعادن والسيراميك وأشباه الموصلات. ومع ذلك، تتطلب هذه العملية بيئة عالية التفريغ وحساسة للغاية للعوامل البيئية، مما قد يحد من قابليتها للتطبيق في سيناريوهات معينة.
ترسيب الاخرق
الترسيب بالترسيب الاخرق هو تقنية ترسيب بالبخار الفيزيائي (PVD) متطورة تتضمن قصف مادة مستهدفة بجسيمات عالية الطاقة، وعادةً ما تكون أيونات من البلازما. ويتسبب هذا القصف في طرد المادة المستهدفة للذرات أو الجزيئات التي تنتقل بعد ذلك عبر الفراغ وتتكثف على الركيزة لتشكل طبقة رقيقة. وهذه العملية متعددة الاستخدامات، ويمكن تطبيقها على مجموعة واسعة من المواد بما في ذلك المعادن والأكاسيد والنتريدات.
في الترسيب بالرش، يتم تعريض المادة المستهدفة للبلازما، وغالباً ما تتكون من أيونات الأرجون والإلكترونات. تقوم هذه الجسيمات النشطة "بإزالة" الذرات من الهدف، مما يؤدي إلى تكوين سحابة من ذرات المصدر. ثم تتكثف هذه السحابة على الركيزة حيث تشكل طبقة رقيقة. ويؤثر اختيار المادة المستهدفة وظروف البلازما بشكل كبير على خصائص الفيلم المترسب.
وأحد الجوانب الملحوظة في الترسيب بالرش هو ظاهرة إعادة الترسيب، حيث يمكن إعادة انبعاث المادة المترسبة بالفعل عن طريق القصف الأيوني أو الذري اللاحق. ويمكن أن يؤثر ذلك على تجانس وسماكة الفيلم، مما يتطلب تحكمًا دقيقًا في معلمات الترسيب لتحقيق النتائج المرجوة.
ويُستخدم الترسيب بالترسيب الاخرق على نطاق واسع في مختلف الصناعات نظرًا لقدرته على إنتاج أفلام عالية الجودة وكثيفة مع التصاق ممتاز بالركيزة. وهي مفضلة بشكل خاص لقابليتها للتطبيق على مجموعة واسعة من المواد، مما يجعلها أداة متعددة الاستخدامات في تصنيع الأغشية الرقيقة المتقدمة للإلكترونيات والبصريات والمكونات الميكانيكية.
الترسيب النبضي بالليزر (PLD)
الترسيب النبضي بالليزر النبضي (PLD) هو عملية تبخير متطورة تستخدم نبضات ليزر عالية الطاقة لتبخير مادة مستهدفة داخل غرفة مفرغة. هذه الطريقة بارعة بشكل خاص في تحضير المواد الرقيقة المعقدة، مما يجعلها الخيار المفضل في مختلف التطبيقات العلمية والصناعية.
تبدأ عملية PLD باستهداف شعاع الليزر للمادة، مما يؤدي إلى تبخيرها وتشكيل عمود من البلازما. ثم تترسب هذه البلازما على ركيزة حيث تتكثف لتشكل طبقة رقيقة. ويتطلب تعقيد هذه العملية، التي تنطوي على التبخر والاستئصال وتكوين البلازما والتقشير، تحسينًا دقيقًا. وعلى الرغم من الوقت والجهد المتزايدين المطلوبين لإدارة المتغيرات العديدة التي تنطوي عليها هذه العملية، فإن الترسيب بالليزر النبضي (PLD) يوفر العديد من المزايا.
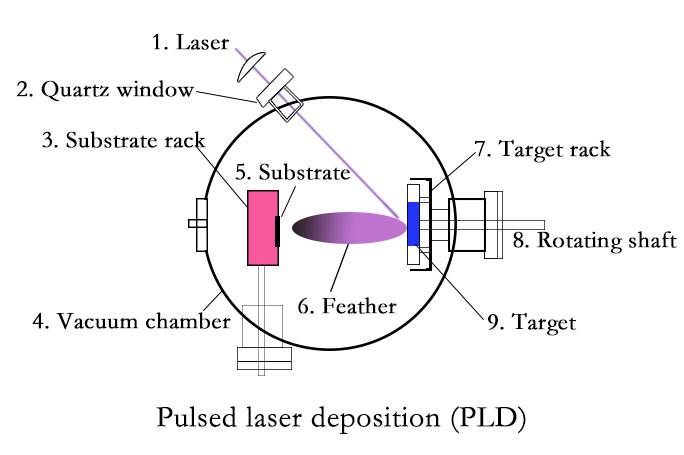
تتمثل إحدى المزايا الرئيسية لجهاز PLD في معدلات الترسيب العالية التي يتميز بها والتي تبسط العملية بشكل كبير مقارنة بالطرق الأخرى. بالإضافة إلى ذلك، يلغي PLD الحاجة إلى الخيوط، مما يبسط الصيانة ويقلل من مصادر التلوث المحتملة. وهذا يجعل تقنية PLD مناسبة بشكل خاص للتطبيقات التي تتطلب دقة ونقاء عاليين، كما هو الحال في صناعات الإلكترونيات والبصريات.
وباختصار، في حين أن تعقيد تقنية PLD يتطلب تحكمًا دقيقًا، فإن قدرتها على إنتاج أغشية رقيقة معقدة وعالية الجودة بكفاءة وبأقل قدر من الصيانة يجعلها أداة قيمة في مجال عمليات الطلاء بالترسيب الكيميائي بالبخار.
ترسيب البخار الكيميائي (CVD)
في حين يختلف الترسيب الكيميائي بالبخار الكيميائي (CVD) اختلافًا جوهريًا عن الترسيب الفيزيائي بالبخار (PVD)، إلا أن هناك حالات يتم فيها الجمع بين هاتين التقنيتين لتحقيق خصائص غشاء متفوقة. تشتهر تقنية الترسيب بالتفريغ القابل للتفريغ (CVD)، وهي طريقة ترسيب بالتفريغ، بإنتاج مواد صلبة عالية الجودة وعالية الأداء، خاصةً الأغشية الرقيقة المستخدمة في صناعة أشباه الموصلات. تتضمن هذه العملية تعريض رقاقة (ركيزة) لواحد أو أكثر من السلائف المتطايرة، والتي تتفاعل و/أو تتحلل على سطح الركيزة لتشكيل الترسيب المطلوب. هذه الطريقة متعددة الاستخدامات وقادرة على ترسيب المواد في أشكال مختلفة، بما في ذلك البنى أحادية البلورية ومتعددة البلورات وغير المتبلورة والفوقية.
وعلى النقيض من تقنية الحرق بالبطاريات البلمرة بالبطاريات البصرية التي تعتمد على العمليات الفيزيائية مثل التبخير أو الرش بالرش، تستفيد تقنية الحرق بالبطاريات البلمرة بالبطاريات القابلة للقنوات CVD من التفاعلات الكيميائية لترسيب المواد. ويسمح هذا النهج الكيميائي بتحكم أكبر في تكوين وخصائص الفيلم المترسب. ومع ذلك، في بعض التطبيقات، يمكن أن ينتج عن الاستخدام التكميلي للتقنية CVD والتقنية بالتقنية البصرية بالتقنية البصرية بالتقنية البصرية أفلامًا ذات خصائص محسنة، مثل تحسين الالتصاق أو تحسين الخصائص الميكانيكية أو طلاءات أكثر اتساقًا. على سبيل المثال، يمكن استخدام الطبقات الأولية للتفريد بالطباعة بالبطاريات البولي فينيل إلكتروني لإنشاء سطح أكثر تقبلاً للطبقات اللاحقة للتفريد بالطباعة بالبطاريات البولي فينيل إلكتروني، وبالتالي تحسين جودة الفيلم بشكل عام.
ويُعد دمج تقنية CVD مع تقنية PVD مفيدًا بشكل خاص في عمليات التصنيع الدقيق المعقدة، حيث يمكن للجمع بين تقنيات الترسيب الكيميائي والفيزيائي معالجة تحديات محددة لا يمكن لأي من الطريقتين التعامل معها بمفردها. ولا يوسع هذا النهج الهجين نطاق المواد التي يمكن ترسيبها فحسب، بل يعزز أيضًا من وظائف المنتج النهائي وأدائه.
استخدام الغازات في عملية الترسيب بالطباعة بالبطاريات البفديوكيميائية
الغازات الخاملة
تلعب الغازات الخاملة، مثل الأرغون (Ar) والهيليوم (He)، دورًا حاسمًا في عمليات الترسيب بالرشاش من خلال العمل كغازات حاملة. ويتم تفضيل هذه الغازات لقدرتها على تعزيز كفاءة ترسيب المادة المستهدفة دون التسبب في أي تفاعلات كيميائية. وتضمن هذه الطبيعة غير التفاعلية الحفاظ على نقاء الفيلم المترسب، وهو أمر ضروري لتحقيق طلاءات عالية الجودة.
ولا يقتصر استخدام الغازات الخاملة على ترسيب الرذاذ؛ فهي تُستخدم أيضاً لمنع التفاعلات الكيميائية غير المرغوب فيها التي يمكن أن تؤدي إلى تدهور العينة. وعادةً ما تشمل هذه التفاعلات غير المرغوب فيها الأكسدة والتحلل المائي، والتي عادةً ما تبدأ بوجود الأكسجين والرطوبة في الهواء. ومن خلال استبدال هذه العناصر التفاعلية بغازات خاملة، يتم الحفاظ على سلامة العينة.
ويُعد الأرجون، على وجه الخصوص، الغاز الخامل الأكثر استخدامًا في التطبيقات المختلفة نظرًا لوفرته الطبيعية العالية وتكلفته المنخفضة نسبيًا. وهو يمثل حوالي 1% من الغلاف الجوي للأرض، مما يجعله متاحًا بسهولة للاستخدام الصناعي. وفي حين أن الأرجون هو الأكثر شيوعًا، يمكن أيضًا استخدام الغازات النبيلة الأخرى مثل الهيليوم والنيون اعتمادًا على المتطلبات المحددة للعملية.
وتجدر الإشارة إلى أن مصطلح "الغاز الخامل" يعتمد على السياق. في حين أن الغازات النبيلة غالبًا ما تعتبر خاملة، إلا أنها يمكن أن تتفاعل في ظل ظروف معينة، وإن كان ذلك باحتمالية منخفضة. وترجع هذه الخاصية إلى حد كبير إلى اكتمال أغلفة التكافؤ لهذه الغازات، وهو ما يجعلها غير تفاعلية بشكل عام. ومع ذلك، هذه ليست قاعدة مطلقة، فحتى الغازات النبيلة يمكن أن تشكل مركبات في ظروف معينة.
عند تحديد درجة نقاء الغازات الخاملة، من الشائع الإشارة إلى مستوى التلوث بالأجزاء في المليون (جزء في المليون). على سبيل المثال، مستوى التلوث 100 جزء في المليون يعني أنه من بين كل مليون جزيء من الغاز الخامل، هناك 100 جزيء غريب. وهذا المقياس مهم لضمان فعالية الغاز الخامل في الحفاظ على نقاء الفيلم المترسب.
وباختصار، لا يمكن الاستغناء عن الغازات الخاملة مثل الأرجون والهيليوم في الترسيب الرذاذي وغيرها من العمليات التي يكون فيها الحفاظ على نقاء وسلامة المواد أمرًا بالغ الأهمية. إن طبيعتها غير التفاعلية وتوافرها يجعلها مثالية لمجموعة واسعة من التطبيقات الصناعية.
الغازات التفاعلية
تلعب الغازات التفاعلية دورًا حاسمًا في تحضير الأغشية الرقيقة المختلفة في عمليات الترسيب بالترسيب بالانبعاث البفدي. وتعد هذه الغازات، التي تشمل الأكسجين (O₂) والنيتروجين (N₂) والفلور (F₂)، ضرورية لإنشاء أفلام الأكسيد والنتريد والفلورايد، على التوالي. وغالبًا ما يكون إدخال هذه الغازات التفاعلية ضروريًا لتحقيق التركيب الكيميائي والخصائص المرغوبة في الأغشية المودعة.
على سبيل المثال، عند تحضير أغشية رقيقة من أكسيد الألومنيوم (Al₂O₃)، عادةً ما يتم إدخال الأكسجين كغاز تفاعل. ويضمن ذلك تفاعل ذرات الألومنيوم في طور البخار مع الأكسجين لتكوين طبقة مستقرة وموحدة من أكسيد الألومنيوم. لا يقتصر استخدام الغازات التفاعلية على أكسيد الألومنيوم؛ بل يمتد إلى مواد أخرى أيضًا، مثل نيتريد السيليكون (Si₃N₄) وثاني أكسيد التيتانيوم (TiO₂)، حيث يتم استخدام النيتروجين والأكسجين على التوالي.
يمكن أن يؤثر اختيار الغاز التفاعلي وتركيزه بشكل كبير على خصائص الفيلم، بما في ذلك كثافته وصلابته واستقراره الكيميائي. على سبيل المثال، يمكن أن تؤدي تركيزات الأكسجين الأعلى إلى أفلام أكثر مسامية وأقل كثافة، في حين أن التركيزات الأقل قد تؤدي إلى أكسدة غير كاملة، مما يؤثر على الجودة الكلية للفيلم.
وخلاصة القول، يعد الاستخدام الحكيم للغازات التفاعلية جانبًا حاسمًا في عمليات PVD، مما يتيح إنشاء أغشية رقيقة عالية الأداء ذات خصائص مصممة خصيصًا لمختلف التطبيقات.
الغازات العضوية
في بعض التطبيقات المتخصصة، تلعب الغازات العضوية مثل الإيثيلين والبروبيلين دورًا حاسمًا في تحضير أغشية البوليمر والمركبات. وغالبًا ما يتم إدخال هذه الغازات في عملية PVD لتسهيل تشكيل هياكل أفلام محددة لا يمكن تحقيقها باستخدام الغازات الخاملة أو التفاعلية وحدها.
ويُعد استخدام الغازات العضوية في عمليات PVD مفيدًا بشكل خاص لإنشاء أفلام البوليمر التي تتطلب وظائف كيميائية محددة. على سبيل المثال، يمكن استخدام الإيثيلين لتشكيل أفلام البولي إيثيلين المعروفة بخصائصها الميكانيكية الممتازة ومقاومتها الكيميائية. وبالمثل، يمكن استخدام البروبيلين لصنع أفلام البولي بروبيلين التي تتميز بمقاومة عالية للحرارة والمواد الكيميائية.
وعلاوة على ذلك، يمكن دمج الغازات العضوية مع غازات أخرى لإنشاء أغشية مركبة تُظهر مزيجًا من الخصائص من المكونات العضوية وغير العضوية على حد سواء. ويسمح هذا النهج الهجين بتخصيص خصائص الأغشية، مما يجعل من الممكن تكييف الأغشية لتطبيقات محددة في صناعات مثل الإلكترونيات والبصريات والهندسة الميكانيكية.
وباختصار، فإن دمج الغازات العضوية في عمليات PVD يفتح إمكانيات جديدة لإنشاء أفلام ومركبات بوليمرية متطورة، مما يتيح تطوير مواد ذات خصائص فريدة ومحسنة.
تعديل ضغط الغاز
يلعب ضغط الغاز في عملية PVD دورًا محوريًا في تحديد كل من معدل الترسيب وجودة الفيلم. تؤثر هذه المعلمة بشكل مباشر على سلوك المادة الغازية أثناء انتقالها من الهدف إلى الركيزة.
عند انخفاض ضغط الغاز، تميل المادة الغازية إلى الانتشار بشكل أكثر اتساقًا، مما يؤدي إلى تحسين كثافة وتجانس الفيلم. ويرجع ذلك إلى أن الضغط المنخفض يقلل من التصادمات بين جزيئات الغاز، مما يسمح بعملية ترسيب أكثر انتظامًا. وبالتالي، يُظهر الفيلم الناتج عيوبًا أقل وبنية أكثر اتساقًا.
وعلى العكس من ذلك، يمكن أن يؤدي ارتفاع ضغط الغاز إلى زيادة خشونة الفيلم. وفي ظل هذه الظروف، تتعرض المادة الغازية لتصادمات أكثر تواترًا، مما قد يؤدي إلى تعطيل عملية الترسيب المنظم. وينتج عن ذلك فيلم أقل اتساقًا مع خشونة سطح محتملة أعلى. ومع ذلك، تجدر الإشارة إلى أن الضغوط الأعلى يمكن أن تعزز أيضًا معدل الترسيب، وإن كان ذلك على حساب جودة الفيلم.
ضغط الغاز | جودة الفيلم | معدل الترسيب |
---|---|---|
أقل | تحسين التكثيف والتجانس | أبطأ |
أعلى | زيادة الخشونة | أسرع |
غالبًا ما يتم تحديد ضغط الغاز الأمثل من خلال المتطلبات المحددة للتطبيق، مما يوازن بين الحاجة إلى أغشية عالية الجودة والرغبة في معدلات ترسيب فعالة. هذا التوازن الدقيق أمر بالغ الأهمية لتحقيق الخصائص المطلوبة في المنتج النهائي.
مجالات تطبيق عملية الطلاء بالطباعة بالانبعاثات الكهروضوئية
صناعة الإلكترونيات
في مجال أجهزة أشباه الموصلات والدوائر المتكاملة وشاشات العرض، تلعب عملية الترسيب الفيزيائي للبخار (PVD) دورًا محوريًا في تصنيع الأغشية المختلفة. وعلى وجه التحديد، تُستخدم عملية الترسيب الفيزيائي بالتقنية الفيزيائية لإعداد ثلاثة أنواع أساسية من الأفلام: الأفلام الموصلة والأفلام العازلة والأفلام البصرية.
الأفلام الموصلة
الأفلام الموصلة ضرورية لضمان تدفق التيار الكهربائي داخل الأجهزة الإلكترونية. تُصنع هذه الأغشية عادةً من معادن مثل الألومنيوم والنحاس والذهب، والتي يتم ترسيبها باستخدام تقنيات مثل التبخير الحراري أو التبخير بالتبخير الحراري أو الرش. يمكن أن يؤثر اختيار المعدن وطريقة الترسيب بشكل كبير على توصيل الفيلم والالتصاق والأداء العام.
الأفلام العازلة
من ناحية أخرى، تعتبر الأغشية العازلة ضرورية لمنع حدوث ماس كهربائي وحماية المكونات الحساسة. يشيع استخدام مواد مثل ثاني أكسيد السيليكون (SiO₂) ونتريد السيليكون (Si₃N₄) لإنشاء هذه الأفلام. تسمح عملية PVD بالتحكم الدقيق في سمك الفيلم وتوحيده، وهو أمر حيوي للحفاظ على سلامة الجهاز وموثوقيته.
الأفلام البصرية
تم تصميم الأفلام الضوئية للتحكم في تفاعل الضوء مع سطح الجهاز، مما يعزز وضوح الشاشة ويقلل من الوهج. وغالباً ما تشتمل هذه الأفلام على طلاءات مضادة للانعكاس وطبقات تحسين النفاذية. تتيح عملية PVD إنشاء هذه الأغشية بخصائص بصرية محددة، مثل معامل الانكسار والنفاذية، المصممة خصيصًا لتلبية متطلبات الجهاز.
باختصار، لا يمكن الاستغناء عن عملية PVD في صناعة الإلكترونيات، حيث توفر طريقة متعددة الاستخدامات ودقيقة لإنتاج الأغشية الموصلة والعازلة والبصرية التي تعتبر أساسية للأجهزة الإلكترونية الحديثة.
الأجهزة البصرية
تلعب عملية ترسيب البخار الفيزيائي (PVD) دورًا حاسمًا في تصنيع الطلاءات البصرية التي تُعد ضرورية لتحسين أداء الأجهزة البصرية المختلفة. تشمل هذه الطلاءات الطلاءات المضادة للانعكاس، والأغشية المحسّنة للنفاذية، والطبقات الواقية، وكلها مصممة لتحسين تفاعل الضوء مع سطح الجهاز.
أنواع الطلاءات البصرية
-
الطلاءات المضادة للانعكاس: تم تصميم هذه الطلاءات لتقليل انعكاس الضوء، وبالتالي زيادة كمية الضوء التي تمر عبر السطح البصري. وهذا مهم بشكل خاص في تطبيقات مثل عدسات الكاميرا والنظارات والألواح الشمسية.
-
طلاءات تعزيز النفاذية: صُممت هذه الأغشية لزيادة انتقال أطوال موجية محددة من الضوء، وهو أمر بالغ الأهمية في أجهزة مثل المرشحات البصرية وأجهزة الاستشعار.
-
الطبقات الواقية: تحمي هذه الطلاءات المواد الأساسية من العوامل البيئية مثل الرطوبة والغبار والأضرار الميكانيكية، مما يضمن طول عمر الجهاز البصري وأدائه.
فوائد تقنية PVD في الطلاء البصري
- الدقة: تسمح عملية PVD بالتحكم الدقيق في سماكة الأغشية، وهو أمر بالغ الأهمية لتحقيق الخصائص البصرية المطلوبة.
- المتانة: تُظهر الأجهزة البصرية المطلية بتقنية PVD متانة فائقة مقارنةً بالأجهزة المطلية بطرق أخرى، مما يجعلها مثالية للاستخدام طويل الأمد في بيئات مختلفة.
- تعدد الاستخدامات: يمكن تكييف عملية PVD لإنشاء مجموعة واسعة من الطلاءات التي تلبي الاحتياجات المحددة للتطبيقات البصرية المختلفة.
التطبيقات في الأجهزة البصرية
نوع الجهاز | غرض الطلاء |
---|---|
عدسات الكاميرا | الطلاءات المضادة للانعكاس لتحسين التصوير |
النظارات | طبقات مضادة للانعكاس ومقاومة للخدش |
الألواح الشمسية | طبقات مضادة للانعكاس لزيادة التقاط الطاقة إلى أقصى حد |
مرشحات بصرية | تحسين النفاذية لأطوال موجية محددة |
الحساسات | طبقات واقية لضمان ثبات الأداء |
لا تعمل عملية PVD على تحسين وظائف هذه الأجهزة فحسب، بل تعمل أيضًا على إطالة عمرها التشغيلي، مما يجعلها تقنية لا غنى عنها في الصناعة البصرية.
المكونات الميكانيكية
في مجال المعالجة السطحية للمكونات الميكانيكية، تؤدي عمليات الترسيب الفيزيائي للبخار (PVD) دورًا محوريًا في تعزيز طول العمر التشغيلي والأداء التشغيلي. يتم استخدام تقنيات الترسيب بالترسيب الفيزيائي للبخار (PVD) بدقة لزيادة مقاومة التآكل ومقاومة التآكل ومقاومة الأكسدة لهذه المكونات. ويؤدي ذلك إلى إطالة عمرها التشغيلي بشكل كبير، مما يجعلها أكثر موثوقية ومتانة في البيئات الصناعية الصعبة.
لا يقتصر تطبيق تقنية PVD في المكونات الميكانيكية على إضافة طبقة واقية فحسب، بل يتعلق بدمج علم المواد المتقدمة لإنشاء أسطح يمكنها تحمل الظروف القاسية. على سبيل المثال، غالبًا ما تخضع المكونات في محركات السيارات وتوربينات الطيران والآلات الصناعية لظروف قاسية يمكن أن تؤدي إلى تدهور سريع. ومن خلال تطبيق طلاءات PVD، يتم تحصين هذه المكونات ضد التآكل والتمزق الناجم عن الاحتكاك والتفاعلات الكيميائية والتعرض لدرجات الحرارة العالية.
علاوة على ذلك، يمكن تصميم طلاءات PVD لتلبية المتطلبات المحددة للمكونات الميكانيكية المختلفة. وسواء كانت أداة عالية الدقة في قطاع التصنيع أو جزءًا مهمًا في جهاز طبي، فإن القدرة على تخصيص الطلاء تضمن أداء كل مكون على النحو الأمثل في ظل مجموعة الظروف الفريدة الخاصة به. يتم تحقيق هذا المستوى من التخصيص من خلال تغيير معلمات الترسيب، مثل نوع المادة المستهدفة وضغط الغاز ودرجة الحرارة لضبط خصائص الفيلم الناتج.
باختصار، يُعد استخدام عمليات PVD في المعالجة السطحية للمكونات الميكانيكية استثمارًا استراتيجيًا في تعزيز متانتها وأدائها، مما يساهم في نهاية المطاف في كفاءة وموثوقية التطبيقات الصناعية المختلفة.
الطلاءات الزخرفية
تُعد عملية PVD مفيدة في إنشاء أغشية زخرفية تعزز المظهر الجمالي لمختلف المنتجات. تُستخدم هذه الأفلام، التي تتميز ببريقها المعدني وألوانها النابضة بالحياة، على نطاق واسع في قطاعات مثل المجوهرات والساعات والأدوات المنزلية. وتسمح هذه العملية بالتحكم الدقيق في سُمك الرقائق وتوحيدها، مما يضمن أن المنتج النهائي يفي بالمعايير العالية للجاذبية البصرية والمتانة المطلوبة في هذه الصناعات.
وفي مجال المجوهرات، يوفر طلاء PVD لمسة نهائية متطورة تحاكي مظهر المعادن الثمينة بجزء بسيط من التكلفة. وهذا الأمر مفيد بشكل خاص للإنتاج بكميات كبيرة حيث يكون الحفاظ على المظهر الفاخر أمرًا بالغ الأهمية. من ناحية أخرى، تستفيد الساعات من طلاءات PVD التي لا تعزز جاذبيتها البصرية فحسب، بل توفر أيضًا مقاومة للخدوش والتآكل، مما يطيل من عمر هذه الساعات.
كما تستفيد المنتجات المنزلية، مثل أدوات المطبخ وأدوات الزينة، من طلاء PVD لتحقيق مظهر عصري وأنيق. وتتيح القدرة على دمج ألوان وأنماط مختلفة في الطلاءات مجموعة واسعة من إمكانيات التصميم، مما يجعل من تقنية PVD أداة متعددة الاستخدامات في تصنيع السلع الاستهلاكية.
علاوةً على ذلك، تُعد عملية الطلاء بالطباعة بالانبعاث الفسفوري الرقمي صديقة للبيئة، حيث تعمل في ظروف التفريغ، مما يقلل من النفايات ويقلل من التأثير البيئي المرتبط بطرق الطلاء التقليدية. ويعزز جانب الاستدامة هذا من جاذبيتها في الصناعات التي تتسم بأهمية قصوى من الناحية الجمالية والمسؤولية البيئية.
مزايا وتحديات عملية الطلاء بالتفريغ بالطباعة بالانبعاثات الكهروضوئية
المزايا
تقدم عمليات الطلاء بالتقنية الفائقة بالطباعة بالرقائق الكهروضوئية العديد من المزايا الجذابة التي تجعلها الخيار المفضل في مختلف الصناعات. تتمثل إحدى أهم هذه المزايا في إنتاجأفلام عالية الجودة. تُظهر هذه الأفلام قدرة استثنائية علىالتصاق استثنائي,والتجانسوالسلامة الهيكليةوالتي تعتبر ضرورية لتحسين أداء المواد المطلية. على سبيل المثال، في صناعة الإلكترونيات، تضمن الأغشية الموصلة المغلفة بالطبقة الموصلة بالطباعة بالقطع PVD توصيلًا كهربائيًا فائقًا وأقل فقدان للإشارة، بينما في الأجهزة البصرية، توفر الطلاءات خصائص بصرية دقيقة تعزز أداء الجهاز.
ميزة أخرى ملحوظة هيالملاءمة البيئية لعمليات PVD. فعلى عكس بعض طرق الطلاء الأخرى، تعمل تقنية PVD في ظل ظروف التفريغ، مما يقلل من إطلاق المواد الضارة في البيئة. وهذا يجعل من تقنية PVD خيارًا مستدامًا، خاصةً في الصناعات التي تكون فيها اللوائح البيئية صارمة. وعلاوة على ذلك، يضمن استخدام الغازات الخاملة مثل الأرجون والهيليوم الحفاظ على نقاء الأغشية دون إدخال أي منتجات ثانوية تفاعلية يمكن أن تضر بالبيئة.
تعدد الاستخداماتتعدد الاستخدامات لعمليات PVD هي أيضًا نقطة قوة رئيسية. يمكن تطبيق تقنية PVD على مجموعة واسعة من المواد، بما في ذلك المعادن والسيراميك والبوليمرات، مما يجعلها مناسبة لتطبيقات متنوعة. وسواء كان الأمر يتعلق بإعداد أغشية رقيقة لأشباه الموصلات أو تعزيز متانة المكونات الميكانيكية أو إنشاء طلاءات زخرفية للمنتجات الاستهلاكية، فإن تقنية PVD توفر حلاً مرنًا يمكن تصميمه لتلبية احتياجات محددة. على سبيل المثال، يسمح استخدام الغازات التفاعلية مثل الأكسجين والنيتروجين بإنشاء أغشية أكسيد ونتريد معقدة، مما يوسع نطاق التطبيقات الممكنة بشكل أكبر.
وباختصار، فإن الجمع بين إنتاج الأفلام عالية الجودة والاستدامة البيئية وقابلية التطبيق الواسعة يجعل من عمليات الطلاء بالتقنية البفدي تقنية مفيدة للغاية في قطاعات متعددة.
التحديات
يتمثل أحد التحديات الأساسية المرتبطة بعمليات الترسيب الفيزيائي للبخار الفيزيائي (PVD) فيتكلفة المعدات. تتطلب الأنظمة المتقدمة للترسيب الفيزيائي بالترسيب بالطباعة بالطباعة بالهيدروجين (PVD)، مثل تلك التي تستخدم التبخير بالحزمة الإلكترونية أو الترسيب النبضي بالليزر، آلات متطورة وأنظمة تحكم دقيقة، والتي يمكن أن تكون باهظة التكلفة بالنسبة للعمليات الصغيرة. بالإضافة إلى ذلك، تتطلب صيانة ومعايرة هذه الأنظمة خبرة متخصصة، مما يساهم في زيادة التكلفة الإجمالية.
هناك تحدٍ حاسم آخر يتمثل فيمعدلات الترسيب. يعد تحقيق معدلات الترسيب المثلى أمرًا بالغ الأهمية للإنتاج الفعال، ولكن يمكن أن يتأثر بعدد لا يحصى من العوامل، بما في ذلك ضغط الغاز ودرجة حرارة الركيزة ونوع المادة المستهدفة المستخدمة. يمكن أن تؤدي معدلات الترسيب الأبطأ إلى إطالة أوقات المعالجة، مما يزيد من تكاليف التشغيل وربما يؤثر على جودة الفيلم المترسب. وعلى العكس من ذلك، قد تؤدي معدلات الترسيب الأعلى إلى أفلام ذات خصائص دون المستوى الأمثل، مثل انخفاض الكثافة أو زيادة الخشونة.
التحكم في سمك الفيلم يمثل أيضًا عقبة كبيرة في عمليات الترسيب بالطباعة بالانبعاث الكهروضوئي. يعد ضمان سماكة موحدة للفيلم عبر الركيزة أمرًا ضروريًا لأداء المنتج النهائي وموثوقيته. ومع ذلك، يمكن أن يكون الحفاظ على التحكم الدقيق في سُمك الفيلم أمرًا صعبًا، خاصةً عند التعامل مع الأشكال الهندسية المعقدة أو الركائز ذات المساحة الكبيرة. يمكن أن تؤدي الاختلافات في السماكة إلى تناقضات في خصائص الفيلم، مثل خصائصه البصرية أو الميكانيكية أو الكهربائية، والتي يمكن أن تكون ضارة بالتطبيق المقصود.
ولمواجهة هذه التحديات، تركز الأبحاث الجارية والتطورات التكنولوجية على تطوير معدات أكثر فعالية من حيث التكلفة، وتحسين معايير الترسيب، وتحسين آليات التحكم في سماكة الفيلم. وتهدف هذه الجهود إلى تعزيز كفاءة وموثوقية عمليات الترسيب الفيزيائي بالبخار السائل، مما يجعلها أكثر سهولة وفعالية في مختلف الصناعات.
اتصل بنا للحصول على استشارة مجانية
تم الاعتراف بمنتجات وخدمات KINTEK LAB SOLUTION من قبل العملاء في جميع أنحاء العالم. سيسعد موظفونا بمساعدتك في أي استفسار قد يكون لديك. اتصل بنا للحصول على استشارة مجانية وتحدث إلى أحد المتخصصين في المنتج للعثور على الحل الأنسب لاحتياجات التطبيق الخاص بك!